Automation: Cobot Adds Interface for Easier Integration With Injection Molding Machines
Universal Robots has developed an Injection Molding Machine Interface (IMMI) supported by EUROMAP 67 and SPI AN-146 communication protocols, simplifying cobot/machine integration.
In response to increased growth in the market, Universal Robots (UR; U.S. headquarters in Ann Arbor, Mich.) has developed an Injection Molding Machine Interface (IMMI) to make communication between its e-Series cobots and molding machines fast and easy. Compatible with EUROMAP 67 and SPI AN-146 communication interfaces, the new IMMI eliminates the need for a hardwired connection with discrete IOs and the development of custom application software to map those IO points coming to and from the injection molding machine. Newer model (made in 2020) e-Series robots using the IMMI can now simply plug in and use a standard interface to communicate.

Universal Robots’ new injection molding machine interface eliminates the need for hardwired connection with discrete IOs.
With the IMMI, UR says molders have the ability to set up, program and control the entire application cycle through the cobot’s teach pendant. The company says the IMMI can be installed into the UR cobots’ control box in less than 10 minutes, using the e-Series control box expansion port for mounting and cable management. To install, a ribbon cable e-connects to the extension bus on the control box, and a 6 meter long cable then connects to the injection molding machine. An IMMI template for the Universal Robots Polyscope operating system is also provided in the programming tree. The IMMI is currently available through UR’s UR+ platform of products certified to work with UR cobots.
Citing market research the company commissioned, UR said in a virtual press conference held to announce the new IMMI that 15% of all cobot applications in 2020 will be in injection molding, automating tasks such as placing inserts into molds and moving parts through post-mold processes.
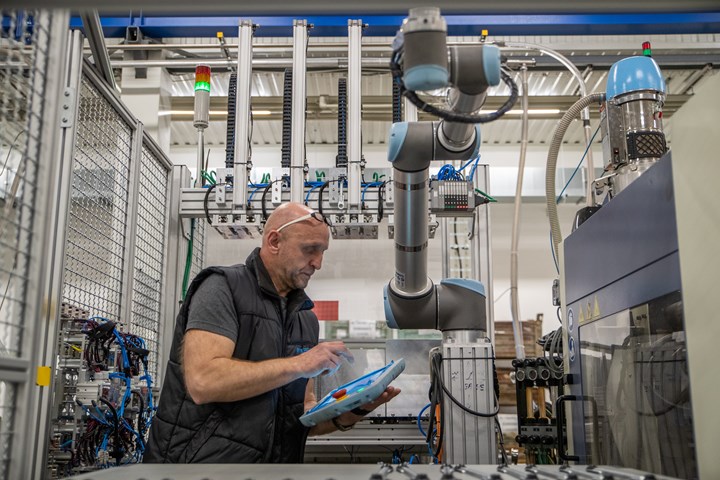
Automotive molder 2K Trend recently deployed a UR10 for machine tending.
Related Content
-
A Systematic Approach to Process Development
The path to a no-baby-sitting injection molding process is paved with data and can be found by following certain steps.
-
Got Streaks or Black Specs? Here’s How to Find and Fix Them
Determining the source of streaking or contamination in your molded parts is a critical step in perfecting your purging procedures ultimately saving you time and money.
-
Process Monitoring or Production Monitoring — Why Not Both?
Molders looking to both monitor an injection molding process effectively and manage production can definitely do both with tools available today, but the question is how best to tackle these twin challenges.