All-Electric Shuttle Debut at NPE
NPE2024: R&B Plastics Machinery’s new small-to-middle-size model is suited for up to six parisons and containers up to 5 L.
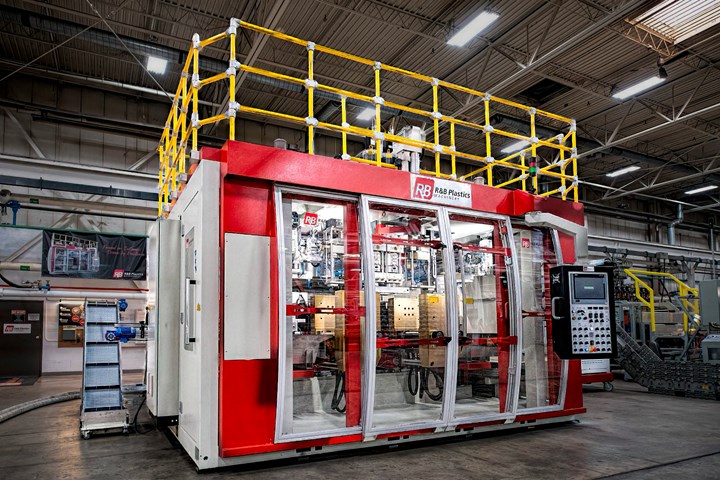
R&B Plastics Machinery is launching its newest all-electric shuttle blow molder at NPE2024. Model RBS-E550D is a double-sided machine with 18-ton clamp and 550-mm stroke. It can be equipped with one to six parisons for containers from 200 ml to 5 L.
The unit on display is running a W. Muller 2 × 250-mm (center distance) trilayer die head with individual servo-electric wall-thickness controls. The machine is also demonstrating W. Muller’s new WM-096 manual screen changer. The main extruder is a 100-mm. 26:1 model designed for processing PE regrind. The satellite extruders for inner and outer layers are 70 mm, 24:1.
The machine has a heavy-walled steel-tube and steel-plate frame with “walk-in” molding area and top-of-machine access platforms for maintenance and mold changes. This is the first R&B shuttle equipped with Yaskawa X absolute servomotors and drives, which offer “some of the fastest and smoothest machine motions available in the industry,” according to R&B.
This new model also provides in-machine deflashing with “center-of-machine” scrap removal, which keeps the conveyor behind the clamp stations and enables for more open area to perform maintenance and mold changes. The in-machine servo-electric part takeout system includes a “center-of-machine” takeaway conveyor for a single-point container exit.
Servo-electric calibration stations with self-adjusting height compensation enable consistent shear-ring cutting. Controls are based on a Siemens IPC477ED industrial PC with 15-in. touchscreen. Remote machine access for technical support is also provided.
Related Content
-
How to Extrusion Blow Mold PHA/PLA Blends
You need to pay attention to the inherent characteristics of biopolymers PHA/PLA materials when setting process parameters to realize better and more consistent outcomes.
-
Blow Molder with a Mission: CKS Packaging Shares Gains Of Its Phenomenal Growth
From three machines in 1986 to 27 plants nationwide today, this family-owned processor has prospered through unwavering customer service, committed employees and dedicated service to its community.
-
Processing Megatrends Drive New Product Developments at NPE2024
It’s all about sustainability and the circular economy, and it will be on display in Orlando across all the major processes. But there will be plenty to see in automation, AI and machine learning as well.