Position Sensor Technology for Closed-Loop Molding
As injection molding machines increasingly seek to respond in real time to shot-to-shot variations in resin viscosity, a new position-sensor technology promises speed and precision.
In order for the screw, mold components and platens of an injection molding machine to adjust their movements in response to a change in resin viscosity, they must first accurately and quickly inform the machine’s controller of their position. To help key machine elements to that end, Novotechnik U.S. Inc., Southborough, Mass., has introduced the Novopad Series TF1 transducer. Instead of applying potentiometers or magnetostriction, this sensor utilizes induction.
Novotechnik says induction technology allows the sensors to maintain position with 1-µm resolution at speeds up 10 kHz, while legacy magnetostrictive technology sensors top out at a 2-kHz update rate for stroke lengths above 250 mm. For magnetostrictive sensors this results from waiting until the magnetic marker hits a return reference point to get a reading. Advanced inductive technology, on the other hand, provides continuous readings from a marker that glides in tracks on the sensors or floats next to them. This not only enables the 10-kHz update rate, but also means the Novopad is touchless and wear free with a maximum acceleration rate of 200 m/sec2.
“By monitoring the viscosity during each shot and dynamically adjusting the injection acceleration, speed and deceleration, better quality can be achieved at faster throughput rates,” Ivan Masek, Novotechnik’s president and CEO says. “A closed loop process is used to adjust on the fly for resin variations, making minute screw-position changes depending on the prior shot’s flow. This calls for a sensor with both speed and precision.”
While magnetostrictive technology uses a waveguide that is inherently subject to vibration errors, for the Novopad machine vibration is virtually eliminated, removing a potential cause for positioning errors that many users aren’t even aware of, according to Novotechnik. Furthermore, since its position is detected by an inductive field, the Novopad is immune to the influence of magnetic fields generated by things like electric motors, hydraulic valve switches or variable frequency drives. It also means the sensor will not attract metal filings and debris. The Novopad can operate in a -40 to 85 C temperature range, and it is available with analog, digital and fieldbus compatible interfaces.
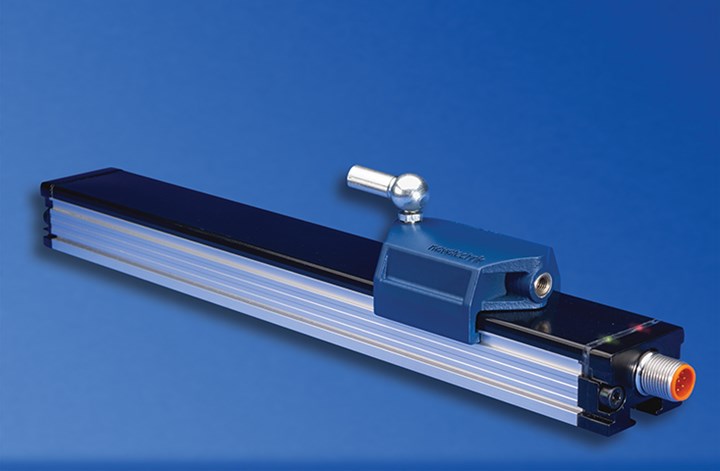
TF1 Series Position Sensors feature a gliding inductive position marker that attaches to your application.
Photo Credit: Novotechnik
Related Content
-
Injection Molding: Focus on these Seven Areas to Set a Preventive Maintenance Schedule
Performing fundamental maintenance inspections frequently assures press longevity and process stability. Here’s a checklist to help you stay on top of seven key systems.
-
Got Streaks or Black Specs? Here’s How to Find and Fix Them
Determining the source of streaking or contamination in your molded parts is a critical step in perfecting your purging procedures ultimately saving you time and money.
-
Use These 7 Parameters to Unravel the Melt Temperature Mystery
Despite its integral role in a stable process and consistent parts, true melt temperature in injection molding can be an enigma. Learning more about these seven parameters may help you solve the puzzle.