Westminster Tool Launches Metal 3D Printing Capabilities
The Connecticut-based moldmaker opened its doors to the public for the first time since the pandemic to celebrate the addition of Mantle’s hybrid metal printing/machining technology.
Industry leaders and state officials gathered at Westminster Tool (Plainfield, Conn.) in January to introduce the company’s new metal 3D printing capabilities. Politicians, educators, administrators and representatives of workforce development organization were among those gathered to see the new Mantle beta machine in action. Mantle’s TrueShape technology prints tool steels from a paste that is dried and machined as it’s laid down, with post-printing sintering used to create solid parts ready for production molding. Westminster Tool has been a beta testing partner for the technology, utilizing it earlier to print a medical forceps tool with conformal cooling.
Supported by Governor Ned Lamont’s Additive Manufacturing Adoption Program (AMAP), Westminster Tool’s equipment purchase was made possible by partnerships with the Department of Economic and Community Development (DECD), the Connecticut Manufacturing Innovation Fund (MIF), and the Connecticut Center for Advanced Technology (CCAT). Last year, Westminster Tool was one of six recipients in the state to be awarded the AMAP grant.
This event was the first time the beta machine was seen up and running by the community as well as by Westminster Tool’s partners and customers. The live demonstration showed Mantle’s unique hybrid additive process building a hardened H13 injection mold cavity with conformal cooling for a complex automotive part.
Among those in attendance were Congressman Joe Courtney, Lieutenant Governor Susan Bysiewicz, Chief Manufacturing Officer Paul Lavoie, and Chief Workforce Officer Kelli Vallieres, along with several members from leading workforce institutions such as CCAT, EWIB and EAMA.
The event was the first time Westminster Tool has opened its doors to the public since before the pandemic, with numerous changes in the intervening years. “We take immense pride in all of the new technology added here and the improvements made on how we train our team on that new technology,” Ray Coombs, Westminster president said in a release. “What makes us unique is our people paired with technology, and that kind of magic deserves to be seen in person.”
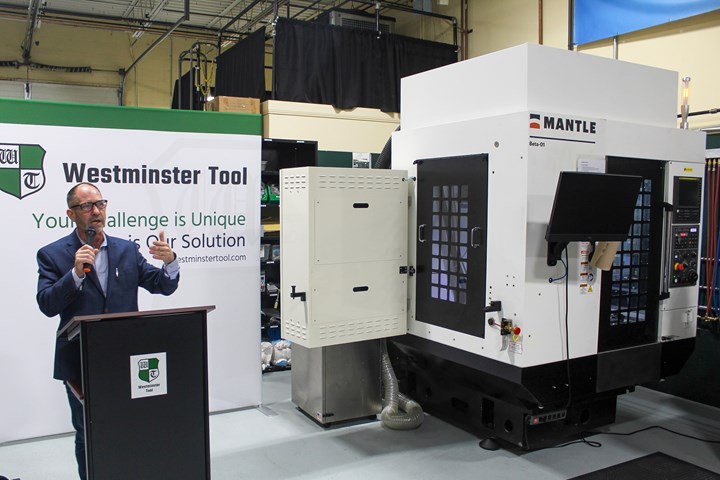
Westminster Tool President Ray Coombs addresses attendees at the moldmakers January event to introduce its new metal 3D printing technology from Mantle.
Photo Credit: Westminster Tool
Related Content
-
Is There a More Accurate Means to Calculate Tonnage?
Molders have long used the projected area of the parts and runner to guesstimate how much tonnage is required to mold a part without flash, but there’s a more precise methodology.
-
Optimizing Pack & Hold Times for Hot-Runner & Valve-Gated Molds
Using scientific procedures will help you put an end to all that time-consuming trial and error. Part 1 of 2.
-
What to Look for in High-Speed Automation for Pipette Production
Automation is a must-have for molders of pipettes. Make sure your supplier provides assurances of throughput and output, manpower utilization, floor space consumption and payback period.