SRC Medical Completes Expansion
The Massachusetts medical injection molder doubled its size with construction of a combined 45,000 ft2 of manufacturing and office space.
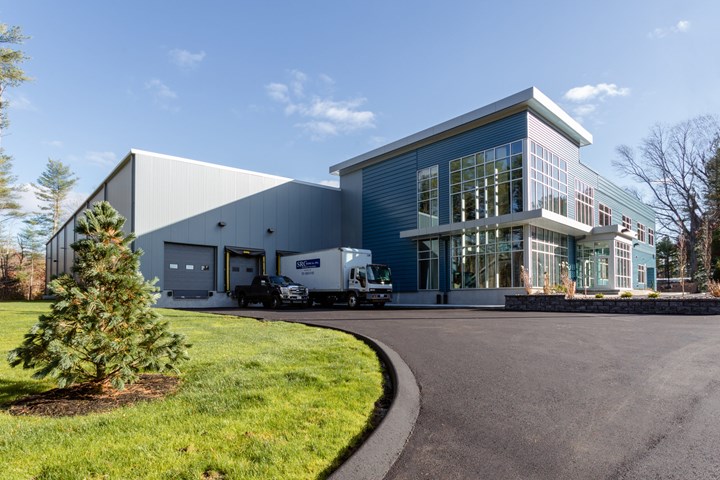
SRC Medical has completed an expansion adding manufacturing and office space.
Photo Credit: SRC Medical
SRC Medical (Hanover, Mass.) has completed construction of an expansion that adds a combined 45,000 ft2 to its footprint, growing both manufacturing and office space. Altogether, the company’s facilities now cover a total of 80,000 ft2. The company has 20-plus injection molding machines, five hot stamping machines, four high-speed wrapping machines, and an in-house machine shop that can maintain and build custom tooling.
A company spokesperson told Plastics Technology that SRC’s existing space will continue to mainly support manufacturing along with its in-house tool room and offices, while the new building will be used as both warehouse space and for manufacturing. At present, the addition has two new 200-ton injection molding machines that were delivered in February to support a new job. The expansion has the capacity to house more than 30 molding machines.
The spokesperson said SRC’s plan is to keep adding molding machines and equipment, with a steady increase of growth in both customers, opportunities and the need for more capacity prompting the investment. “Our current building is extremely close to being maxed out in space,” the spokesperson said.
Founded in 1972 and family owned in its third generation, SRC Medical supplies the medical, healthcare, and consumer goods industries with capabilities in injection molding, hot stamping, assembly, and wrapping, as well as engineering, product development, first article inspection and short-run production. The 大象传媒 is ISO 13485 and CE certified, as well as FDA registered.

SRC Medical’s expansion has space to accommodate more than 30 injection molding machines.
Photo Credit: SRC Medical
Related Content
-
How to Design Three-Plate Molds, Part 1
There are many things to consider, and paying attention to the details can help avoid machine downtime and higher maintenance costs, and keep the customer happy.
-
A Systematic Approach to Process Development
The path to a no-baby-sitting injection molding process is paved with data and can be found by following certain steps.
-
Got Streaks or Black Specs? Here’s How to Find and Fix Them
Determining the source of streaking or contamination in your molded parts is a critical step in perfecting your purging procedures ultimately saving you time and money.