Siemens Expands Digital Ecosystem for IoT ‘Transformation’
New open digital ´óÏó´«Ã½ platform aims to make digital transformation for companies of all sizes faster, easier and scalable.
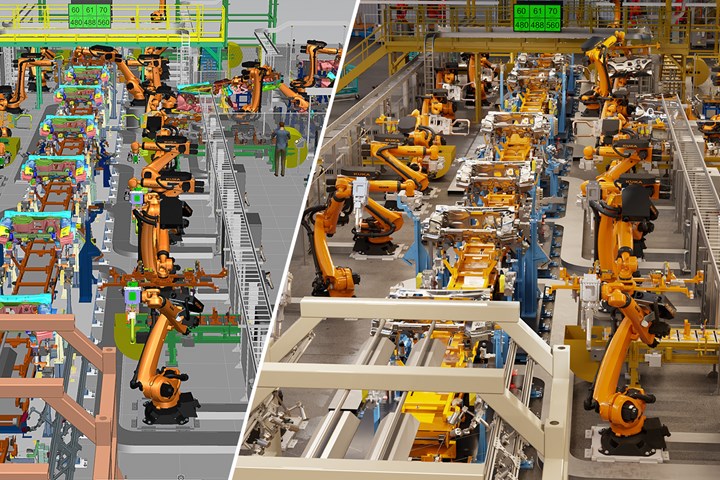
Siemens Process Simulate (left) connects to Nvidia Omniverse (right) for a photorealistic, real-time digital twin of a manufacturing operation. AI and physics-based simulation could help troubleshoot, optimize and run the physical plant. (Image: Siemens & Nvidia)
AG in Germany has launched what it calls “an open digital ´óÏó´«Ã½ platform to accelerate digital transformation.” It is intended to bring the “Internet of Things (IoT),” also called Industry 4.0, to “customers of all sizes,” the company says. However, the scope of Siemens’ ambitions encompasses entire factories as large as automotive assembly plants, city districts, and transportation systems.
This major expansion of the Siemens Xcelerator program utilizes a growing partner “ecosystem” to deploy “a curated program of IoT-enabled hardware, software and digital services following key design principles of interoperability, flexibility, openness and as-a-service,” Siemens says. The last item refers to “software as a service,” meaning a subscription model that minimizes upfront costs and helps keep apps up to date. The “curated” hardware, software and services have been tested for interoperability; more than 50 partner companies have already been certified to participate in this ecosystem. Another planned element of the Xcelerator program is “an evolving marketplace to facilitate interactions and transactions between customers, partners and developers.”
Siemens says it “will transform its entire portfolio of hardware and software to become modular, cloud-connected and built on standard application programming interfaces (APIs).” The ultimate goal is to “combine the real and digital worlds across operational and information technology.” For instance, Siemens will integrate its industrial IoT (IIoT) solutions under the umbrella of Industrial Operations X, with the intent to accomplish “fusion of data from the real world of automation with the digital world of information technology.”
An example of where this is headed can be seen in Siemens’ brand-new partnership with Nvidia of Santa Clara, Calif., a leader in computer graphics, artificial intelligence (AI), and accelerated computing. The two of them plan to create an “industrial metaverse with physics-based digital models from Siemens and AI-enabled, physically accurate, real-time simulation from Nvidia.” The idea is that together, the partners can create a photorealistic “digital twin” of a factory—even a very large one the size of an auto assembly plant—and have the simulated plant operate under the same physical and mechanical constraints as the equipment in the real one, even running the same operating software for the simulated machines and robots and material-handling equipment. That way, the digital twin can mirror in real time what the real plant is doing. According to Siemens, “This is not animation, but simulation, using data from the actual factory.” This can be used to spot and correct inefficiencies—by human manages or technicians, or by software using AI. Notes Jenson Huan, Nvidia cofounder, president and CEO, “AI allows writing software that no human can”—and testing that software too. “We use digital twins to design and simulate and stress test many kinds of products, so why not factories?” He also noted that “AI must make recommendations that obey the laws of physics.” Using Nvidia’s Omniverse collaborative simulation platform, “The live virtual world, or metaverse, will mimic the physical world in full fidelity and in real time.”
Speaking at the press conference, Milan Nedeljkovic, member of the management board of BMW AG, said BMW aims to realize its “iFactory” vision of the factory of the future by linking existing physical systems one by one into an overall digital twin of an assembly plant. Sensors in the physical plant will feed real-time data to the digital twin. The aim, he said, is for “the digital twin to steer the factory.” According to Nedeljkovic, this is part of BMW’s goal to improve manufacturing operational efficiency 30% by 2025.
Related Content
Production Monitoring Automates Molder’s Planning, Operations
DCT saves 60 man-hours per week by shifting from paper records and discrete spreadsheets to a shared, automatic production monitoring platform.
Read MoreWhat to Look for in High-Speed Automation for Pipette Production
Automation is a must-have for molders of pipettes. Make sure your supplier provides assurances of throughput and output, manpower utilization, floor space consumption and payback period.
Read MoreDigital Product Passport Trialed by Henkel Consumer Brands
Joint project between R Cycle and converter Korozo Group is implementing packaging traceability technology.
Read MoreBetter Manufacturing Data Empowers Plastics Processors to Make Better Decisions
What’s needed to take all the data pulled from production planning, production monitoring and quality control systems and put it in the hands of the right people at the right time?
Read MoreRead Next
Beckhoff’s Industry 4.0 Products Integrated With Siemens’ MindSphere
The TwinCAT internet of things (IoT) product family can now be integrated with Siemens industrial IoT-as-a-service platform.
Read More