Rethinking the Radiator Grille: Award-Winning Part Combines Processes
BMW turned to Engel to supply an automated cleanroom cell that combines thermoplastic backmolding of a film and polyurethane processing to create the iX’s SPE 2021 Grand Award winning badge.
The electrification of vehicles has allowed OEMs to make dramatic changes to more than just drivetrains as the functional requirements of battery operated vehicles allow longstanding components to be reimagined.
In the case of BMW, its conversion of a traditional radiator grille into a multifunctional “badge” for the iX sport utility garnered the 2021 Grand Award from the International Society for Plastics Technology (SPE Central Europe).
Molded in a cleanroom atmosphere, the kidney-shaped badge, which applies various Engel technologies, serves an obvious cosmetic function, as part of the car’s visage, but on a functional basis, it also protects cameras and several sensors for assisted driving at present and autonomous operation in the future.
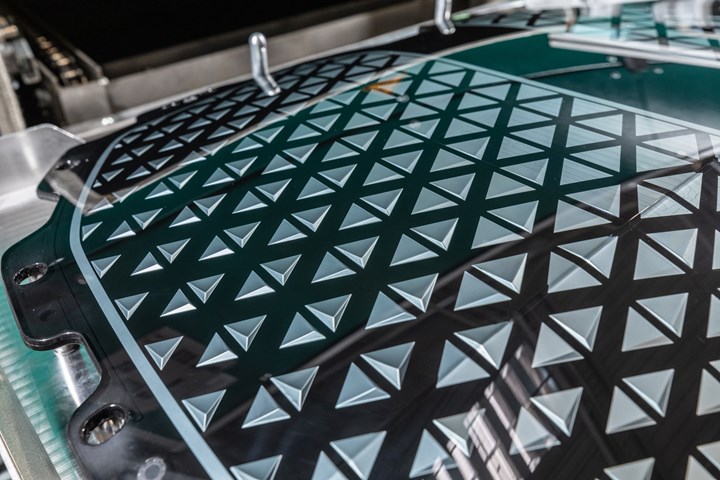
A cleanroom environment is necessary for the production of the BMW iX “badge”, since any dust would be visible through the high-gloss polyurethane finish.
Photo Credit: BMW Group
Produced in an integrated process, the component consists of a functional film that is back-molded with polycarbonate and then flood-coated with polyurethane through a combination of technologies also offered under Engel’s clearmelt portfolio.
While this suite of technologies had been applied for interior components, the BMW iX’s badge marks the first time the combined film back-injection molding and polyurethane flooding were used in series production of functional exterior components, where environmental stresses are even greater.
A Cell Within a Cell
Engel acted as the system supplier for project, making it responsible for the complete production cell, which is located at BMW’s Landshut, Germany production campus. The cell is built around an Engel duo Combi M injection molding machine with a horizontal rotary table; two large articulated robot arms for handling the films and molded parts; a film-cleaning system; an inline quality-control station; and peripheral units including the polyurethane technology, supplied by Hennecke (St. Augustin, Germany).
The molding machine’s clamping unit and the robots are enclosed in a housing measuring more than six meters long and over four meters high (20 by 13 ft), supplied by Petek Reinraumtechnik (Radolfzell, Germany), which creates a ISO Class 7 cleanroom. An Engel spokesperson noted that the cleanroom environment is necessary to avoid any dust on surfaces, which would be visible under the high-gloss polyurethane cover.
When it comes time to change the mold or do any other work in the clamp area, a sliding ceiling above the clamping unit opens up, allowing access to the tool. Within the cleanroom space, all steps, including the unpacking of films, insertion of films into the tool, and part removal are fully automated. Adjoining the ISO Class 7 clean room is an ISO Class 8 greyroom, which acts as a work area for production employees to transfer the functional films, which are enclosed in airtight boxes, into the cleanroom, as well as shepherd along packed, molded parts for downstream processing.
A Virtual Preview
Due to its unique nature, when Engel began quoting the first-of-its-kind cell to the automaker, it didn’t have an existing system in the real world to fully show how the production system would function, so it turned to virtual reality. Engel created a 3D simulation of the production cell to show BMW how the machine and robots would interact and help assess ergonomic and other aspects of production, before construction even began.
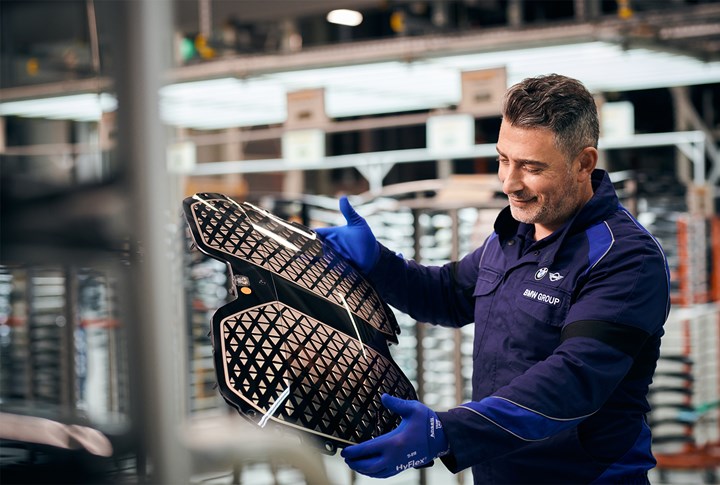
The back-molded film and polyurethane (PUR) coating applied in Engel’s clearmelt technology protect sensitive electronics under a scratch-resistant PUR surface, which also imparts high gloss and depth to the cosmetic part.
Photo Credit: BMW Group
Related Content
How to Extrusion Blow Mold PHA/PLA Blends
You need to pay attention to the inherent characteristics of biopolymers PHA/PLA materials when setting process parameters to realize better and more consistent outcomes.
Read MorePaperless ‘Smart Factory’ Based on Automated Production Monitoring
Tier 1 automotive molder’s home-built production-monitoring and ERP systems, designed for “the little guy,” boost its efficiency rating and profits.
Read MoreWhat to Look for in High-Speed Automation for Pipette Production
Automation is a must-have for molders of pipettes. Make sure your supplier provides assurances of throughput and output, manpower utilization, floor space consumption and payback period.
Read MoreMedical Tubing: Use Simulation to Troubleshoot, Optimize Processing & Dies
Extrusion simulations can be useful in anticipating issues and running “what-if” scenarios to size extruders and design dies for extrusion projects. It should be used at early stages of any project to avoid trial and error and remaking tooling.
Read MoreRead Next
Touch-Sensitive Control Surfaces: The Next Thing in Medical Technology?
Cost savings and cleanability are moving overmolded capacitive-sensing films from automotive consoles into medical equipment.
Read MoreInjection Molding: In-Mold PUR Coating Now Comes in Colors
Colored in-mold PUR coatings can now be added to injection molded auto parts.
Read MoreLead the Conversation, Change the Conversation
Coverage of single-use plastics can be both misleading and demoralizing. Here are 10 tips for changing the perception of the plastics industry at your company and in your community.
Read More