Cellulose Fiber Reinforced PP Targets Automotive
The material is seen as a suitable candidate for use in door module carriers, center consoles, and armrest cores.
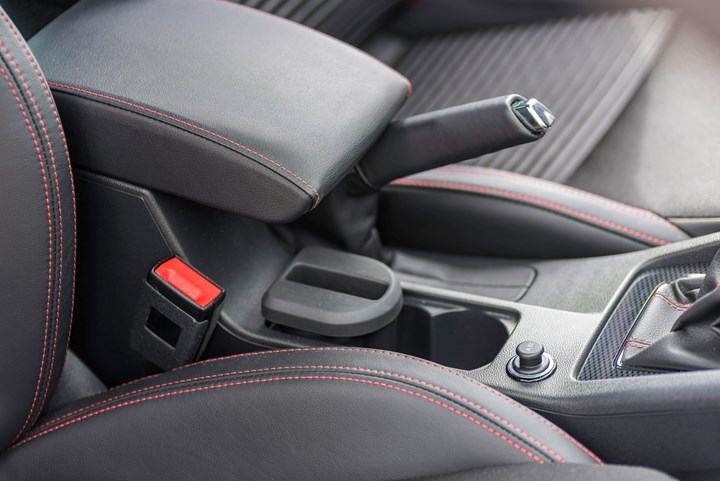
Launched by last year, a long cellulose fiber reinforced PP is being targeted at such automotive applications as door module carriers, center consoles, and armrest cores. Plastron LFT PP reportedly has been shown to offer lower density and reduced greenhouse gas (GHG) emissions than short glass-reinforced resins while delivering the same mechanical properties.
A non-edible biomass raw material derived from organic non-fossil resources, cellulose boasts characteristics such as, negative carbon influence (absorbs carbon dioxide in the air when manufactured) and is sustainable (raw material that can be procured sustainably unlike resources such as natural minerals). Plastron LFT, specifically, incorporates regenerated cellulose fibers made using the solvent method which produces hardly any waste. Polyplastics uses a solvent method cellulose fiber that is said to emit less greenhouse gas when manufactured compared to typical glass fiber. Since it has nearly 10% lower density than glass fiber reinforced PP resin, its greenhouse gas emissions are also even lower when compared in equal volumes.
A significant majority of typical regenerated cellulose is manufactured using a complex process which involves modification of the cellulose followed by dissolving in solvent and spinning and finally restoring the original cellulose form. This process results in significant emissions of greenhouse gases including carbon dioxide. In contrast, the solvent method used by Polyplastics is a closed process that reportedly recovers virtually 100% of the solvent. It generates minimal waste and produces materials that are even more eco-friendly. The company has earned multiple patents throughout the world for resins reinforced with long-regenerated cellulose fiber, including solvent method cellulose fiber.
Related Content
-
Delivering Increased Benefits to Greenhouse Films
Baystar's Borstar technology is helping customers deliver better, more reliable production methods to greenhouse agriculture.
-
Fundamentals of Polyethylene – Part 5: Metallocenes
How the development of new catalysts—notably metallocenes—paved the way for the development of material grades never before possible.
-
Polyethylene Fundamentals – Part 4: Failed HDPE Case Study
Injection molders of small fuel tanks learned the hard way that a very small difference in density — 0.6% — could make a large difference in PE stress-crack resistance.