Polyolefin Pressure Pipe Can Now be Biaxially Oriented
Technology introduced by SABIC reportedly improves properties across the board and cuts resin use by at least 30%.
You’ve heard of biaxially oriented film? Well, now there is a way to stretch polyolefin pressure pipe too.
Resin giant SABIC has introduced new PE and PP resins and is collaborating with Italian pipe extrusion builder Tecnomatic and processor Aquatherm of Germany on technology to improve the properties of polyolefin pressure pipe for potable water and sanitation applications, all while cutting resin usage.
The technology is straightforward: pipe is first conventionally extruded with thick walls and small dia, then drawn over a heated mandrel and stretched in two directions to yield a larger-dia pipe with thinner walls. has installed a fully integrated biax pipe extrusion line in Italy for evaluation, trials and optimization of the process with dedicated SABIC resins.
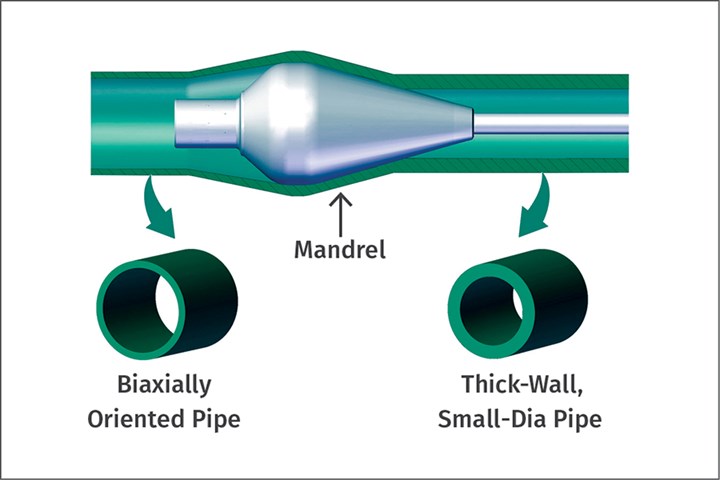
SABIC’s says the new technology offers substantial improvements over current polyolefin pipe across the entire range of performance criteria. Higher resistance against internal pressure enables wall-thickness reduction and can reduce material use by at least 30%, the resin producer says. Superior resistance to slow-crack growth facilitates pipe installation by making it unnecessary to dig trenches. What’s more, the very smooth inner wall surface reduces the energy required for pumping. The technology renders the pipes more abrasion resistant and prolongs their lifetime, says SABIC.
In addition, the new PE and PP pipes promise better resistance to disinfectants, a lower coefficient of linear thermal expansion and improved low-temperature impact strength, according to SABIC.
Polyolefin pipe processor is planning on introducing biaxially pressure pipe for a variety of applications. The processor has a sales office in Linden, Utah.
SABIC introduced the technology last September at the International Plastic Pipes XX Conference and Exhibition in Amsterdam.
Related Content
-
Part 2 Medical Tubing: Use Simulation to Troubleshoot, Optimize Processing & Dies
Simulation can determine whether a die has regions of low shear rate and shear stress on the metal surface where the polymer would ultimately degrade, and can help processors design dies better suited for their projects.
-
How to Select the Right Tooling for Pipe Extrusion
In pipe extrusion, selecting or building a complementary set of tooling often poses challenges due to a range of qualitative factors. Here’s some guidance to help you out.
-
Understanding Melting in Single-Screw Extruders
You can better visualize the melting process by “flipping” the observation point so the barrel appears to be turning clockwise around a stationary screw.