PET Cap and Closure Manufacturing System Launches
NPE2024: Origin Materials and partner Packsys Global say the high-throughput system opens the door to monomaterial bottles, promoting recycling and easing end of life for the package.
Origin Materials, Sacramento, California, which introduced a PET cap in 2023, has partnered with Brückner Group company PackSys Global, a Swiss-based maker of plastic closure slitting machines, on a PET cap and closure manufacturing system. After conducting successful tests of the system at the PackSys’ KREALAB technology center located in its Rüti, Switzerland, headquarters, the companies are showcasing the results at NPE2024.
PackSys is featuring its TEM-SF Plus slitting and folding machine and its capLAB+ inline unit for checking the tear-off force of the tamper-evident tape (TE tape) on closures. That system is running at Netstal’s booth where it is integrated into an INTRAVIS CapWatcher System and is being presented together with a Netstal injection molding machine. Packsys and Origin representatives are split between the Brückner Group USA’s and Netstal’s booths. Packaging supplier Berry Global is also an onsite partner.
Caps are traditionally injection molded or compression molded from HDPE or PP, complicating end-of-life recycling for PET bottles. At this time, a spokesperson for Origin declined to say how the PET caps are initially produced but noted that any PET, including recycled or its own biobased PET, can be used in its production system. Origin also notes that PET offers better oxygen and carbon dioxide barrier than HDPE and PP.
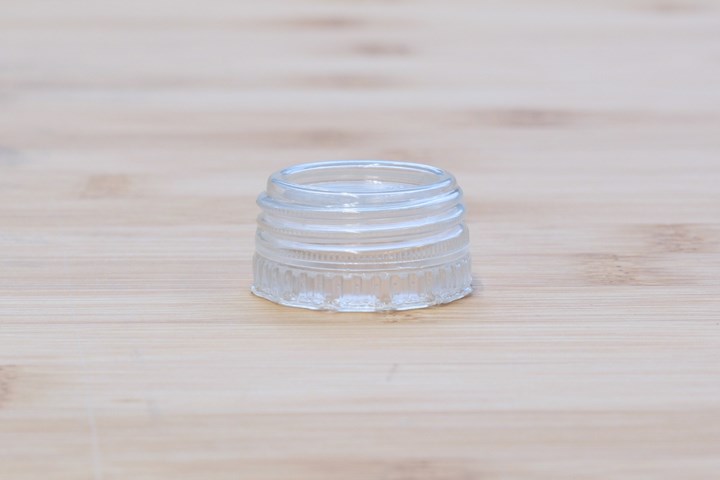
Origin Materials and PackSys Global is detailing a production system for PET caps and closures at NPE2024. Source: Origin Materials
Related Content
-
PHA Compound Molded into “World’s First” Biodegradable Bottle Closures
Beyond Plastic and partners have created a certified biodegradable PHA compound that can be injection molded into 38-mm closures in a sub 6-second cycle from a multicavity hot runner tool.
-
How to Optimize Injection Molding of PHA and PHA/PLA Blends
Here are processing guidelines aimed at both getting the PHA resin into the process without degrading it, and reducing residence time at melt temperatures.
-
Foam-Core Multilayer Blow Molding: How It’s Done
Learn here how to take advantage of new lightweighting and recycle utilization opportunities in consumer packaging, thanks to a collaboration of leaders in microcellular foaming and multilayer head design.