One-Step Method for Blow Molding Composites
Lanxess forms and bonds Tepex composite sheet to a blow molded parison in the mold.
Now there’s a one-step method of forming lightweight structural thermoplastic hollow sections or hollow articles locally reinforced with continuous fibers. At its German technical center, the High Performance Materials (HPM) ´óÏó´«Ã½ unit of Lanxess is developing methods of placing preheated blanks of composite organosheets in an extrusion blow mold while a parison of the same thermoplastic material is being extruded. When the mold closes and the parison is inflated, the organosheet is formed to shape by the mold and bonded tightly to the parison by the blowing pressure.
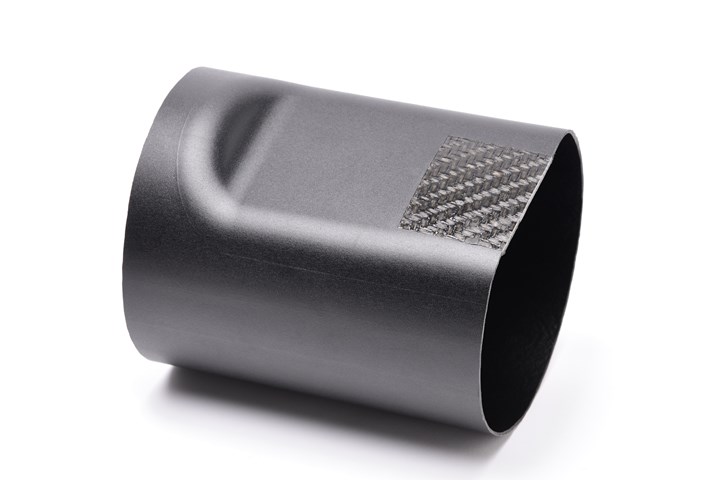
Good adhesion between the blow molded parison and Tepex continuous-fiber organosheet allows full utilization of the composite’s strength and stiffness.
The process uses resin-impregnated, continuous-fiber fabrics from Lanxess’ Bond-Laminates ´óÏó´«Ã½. These organosheets can be of nylon 6 or 66 (or other resins) reinforced with continuous carbon, glass or aramid fibers. These sheets reportedly bond well in blow molding with Lanxess’ Durethan high-viscosity blow molding grades of nylons 6 and 66 with and without glass fibers. “Even low blow molding pressures are enough to form Tepex into critical 3D geometries such as hemispheres with tight radii,” says Tilmann Sontag, expert in lightweight design at HPM’s Tepex Automotive Group. He adds that the fabric reinforcement makes heated Tepex blanks much easier to handle than unidirectional tapes.

Engineering plastics experts Tilmann Sontag (l.), Loreen Winkelake and Arthur Rieb experiment with blow molding composites at the Dormagen technical center of Lanxess’ HPM unit.
Previously, blow molding with composite sheets required welding flat or preformed Tepex blanks onto the part after blow molding, thus adding one or two extra steps. The new one-step process boasts cycle times “that are typical of blow molding,” states Arthur Rieb, HPM blow molding specialist. The blow molding step determines the overall cycle time.
Related Content
-
PolyJohn Turns to Blow Molding, Doubles Its Productivity
Leading maker of portable sanitation products knew thermoforming, sheet extrusion, rotomolding and injection molding. Then it found the missing link to higher productivity and new markets: blow molding.
-
Multilayer Solutions to Challenges in Blow Molding with PCR
For extrusion blow molders, challenges of price and availability of postconsumer recycled resins can be addressed with a variety of multilayer technologies, which also offer solutions to issues with color, processability, mechanical properties and chemical migration in PCR materials.
-
Blow Molder with a Mission: CKS Packaging Shares Gains Of Its Phenomenal Growth
From three machines in 1986 to 27 plants nationwide today, this family-owned processor has prospered through unwavering customer service, committed employees and dedicated service to its community.