New HDPE Pipe Processor Goes ‘QuickSwitch’ Route
Encoma of Canada installs KraussMaffei’s first-ever QuickSwitch line in North American to maximize pipe production flexibility, with more capacity on the way.
Derek Hofer had clear goals in mind when he took over as plant manager for startup HDPE pipe producer Encoma Ltd at its 63,000 ft2 plant in Manitoba, Canada: no simple me-too products, but state-of-the art high-end extrusion technology to allow the processor to make high-quality pipe as efficiently as possible.
The search led Hofer in late 2021 to install the first QuickSwitch line KraussMaffei ever installed in North America. So satisfied was Hofer was with that decision that he has since placed orders for two additional production line.
Encoma started manufacturing multilayer HDPE pipes for water supply, geothermal and cable protection applications, and underfloor heating in the fall of 2021 after building a new plant in Manitoba. KraussMaffei Extrusion installed a complete three-layer QuickSwitch line covering the entire production process—from raw material to semi-finished product handling.
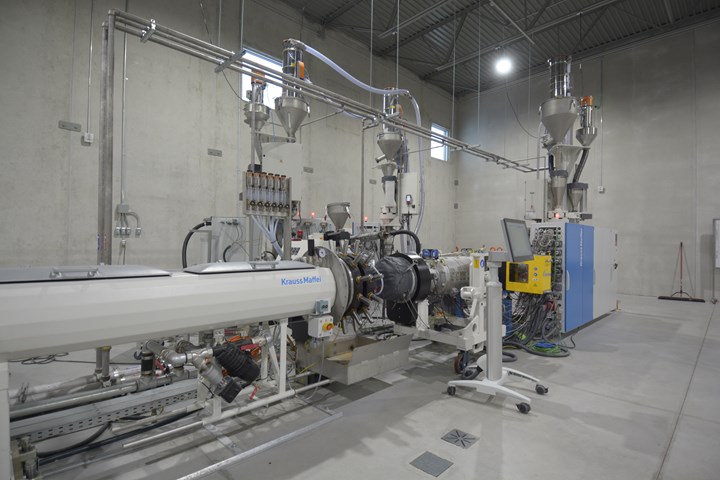
KraussMaffei installed the first-ever QuickSwitch line for HDPE pipe at startup company Encoma in Canada. Photo: KraussMaffei
“For us as a newcomer in this industry, it was extremely important to have a competent partner at our side who would be able to set up a turnkey plant on our premises and also provide training and support,” says Hofer. KraussMaffei fully met all expectations, he adds, which encouraged Encoma to order a second QuickSwitch line, along with a 5-layer line specifically designed for underfloor heating pipes. “Quality, reproducibility and production time achieved with the first QuickSwitch line for HDPE pipes were so convincing that we decided to go straight back to KraussMaffei as our machine supplier,” explains Hofer.
QuickSwitch is the name of KraussMaffei Extrusion's unique package solution for the flexible production of pipes of widely differing dimensions on one line without requiring any retooling. The core component of each QuickSwitch line is an adjustable calibration basket that is set to new pipe dimensions fully automatically and within a given time without having to stop the production line. The waste produced during the “quick switch” period is limited to a cone-shaped piece of material, which contributes not only to higher efficiency but also to enhanced sustainability in hose production.

With QuickSwitch technology, an adjustable calibration basket allows pipe diameters to be changed automatically without having to stop the line or change any tooling. Photo: KraussMaffei
In addition to changing the pipe dimensions at the push of a button, QuickSwitch also ensures fine adjustment of pipe wall thickness and pipe centering. Both parameters are critically important in the production of high-quality pipes. Once saved, production data can be retrieved and adjusted at any time, which ensures exact reproducibility.
The entire downstream equipment integrated into the control system is automatically adjusted as well, rendering readjustments unnecessary. Thanks to the intelligent control system, all production parameters can be monitored, documented and correlated with each other. As a result, the line manages itself and operator effort is minimal.
With the line already installed at the Manitoba site, Encoma produces pipes in diam. ranging between 1-2.5 in. The second line will extend the range to more than 6 in. “Thanks to the perfectly tailored machine solution, we are able to produce a wide range of different pipes for changing customer requirements even in small quantities,” states Hofer.
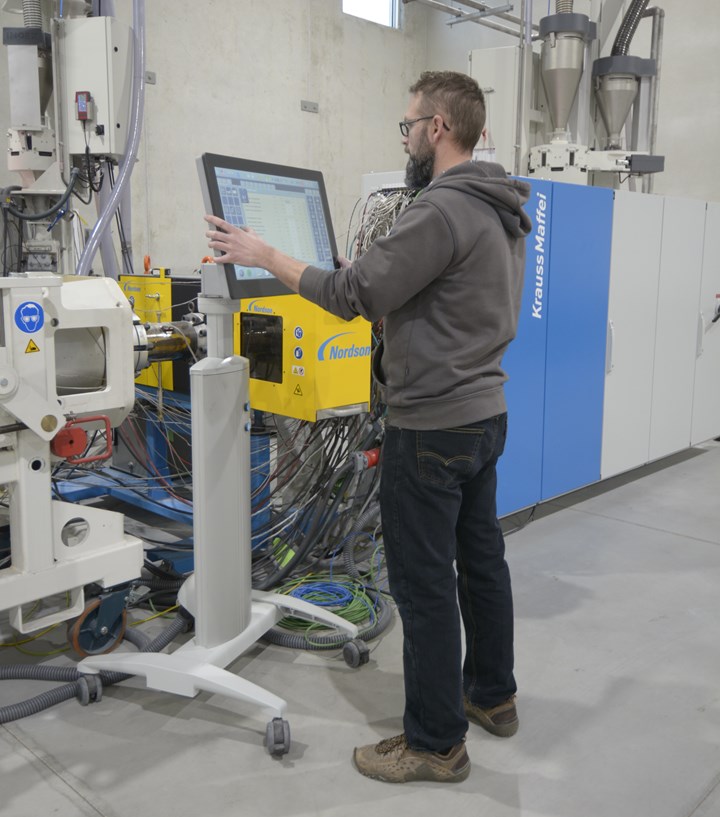
QuickSwitch lets operators make changes in pipe dimensions and fine tune pipe wall thickness and centering at a push of a button. Photo: KraussMaffei
Related Content
Why Are There No 'Universal' Screws for All Polymers?
There’s a simple answer: Because all plastics are not the same.
Read MoreWhat to Know About Your Materials When Choosing a Feeder
Feeder performance is crucial to operating extrusion and compounding lines. And consistent, reliable feeding depends in large part on selecting a feeder compatible with the materials and additives you intend to process. Follow these tips to analyze your feeder requirements.
Read MoreThe Importance of Barrel Heat and Melt Temperature
Barrel temperature may impact melting in the case of very small extruders running very slowly. Otherwise, melting is mainly the result of shear heating of the polymer.
Read MoreHow to Select the Right Tooling for Pipe Extrusion
In pipe extrusion, selecting or building a complementary set of tooling often poses challenges due to a range of qualitative factors. Here’s some guidance to help you out.
Read MoreRead Next
Making the Circular Economy a Reality
Driven by brand owner demands and new worldwide legislation, the entire supply chain is working toward the shift to circularity, with some evidence the circular economy has already begun.
Read MoreBeyond Prototypes: 8 Ways the Plastics Industry Is Using 3D Printing
Plastics processors are finding applications for 3D printing around the plant and across the supply chain. Here are 8 examples to look for at NPE2024.
Read MoreLead the Conversation, Change the Conversation
Coverage of single-use plastics can be both misleading and demoralizing. Here are 10 tips for changing the perception of the plastics industry at your company and in your community.
Read More