New Cap for Child-Resistant Pill Bottles Is Senior-Friendly & Saves Resin
Exclusive lightweight cap design can be removed simply pushing down on the center. No gripping or twisting needed.
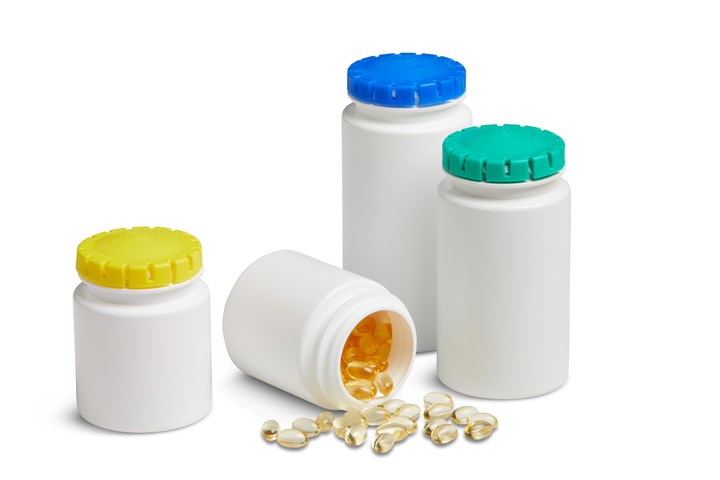
New Pop & Click Cylinders from Drug Plastics come in 60 to 120 cc and use 22% to 27% less plastic than conventional bottles with push-and-turn closures. (Photo: Drug Plastics Group)
“Pop & Click” is a novel child-resistant closure system from , Boyertown, Pa. (drugplastics.com), that offers benefits in usability by seniors and other persons with limited finger mobility—and in manufacturing sustainability. Pressing on the dome in the center of the cap with a finger or knuckles or heel of the hand causes the “petals” on the circumference of the cap to release and lift up, freeing the cap. The cap can be replaced by pressing it onto the top of the bottle—no twisting or gripping is required. The closure system is ASTM tested and CPSC approved for child resistance.
Pop & Click Cylinders are available in sizes of 60, 100 and 120 cc for packaging pills, tablets, capsules and cannabis products. The cylinders have a special 38-mm finish and are blow molded of FDA-approved virgin or post-consumer recycled (PCR) HDPE. The exclusive closure is injection molded of FDA-approved virgin PP. They come standard with a molded TPE reseal liner that functions as a gasket to protect the package contents. A heat induction liner is optional.
The closures use almost 65% less resin than a standard two-piece, push-and-turn closure. Depending on size, the overall package uses 22% to 27% less plastic than standard designs, according to Drug Plastics.
Related Content
-
Optimizing Pack & Hold Times for Hot-Runner & Valve-Gated Molds
Using scientific procedures will help you put an end to all that time-consuming trial and error. Part 1 of 2.
-
Back to Basics on Mold Venting (Part 1)
Here’s what you need to know to improve the quality of your parts and to protect your molds.
-
Use These 7 Parameters to Unravel the Melt Temperature Mystery
Despite its integral role in a stable process and consistent parts, true melt temperature in injection molding can be an enigma. Learning more about these seven parameters may help you solve the puzzle.