Nalgene Bottle Production Completes Conversion to Certified 50% Recycled Material
Nalgene Outdoor has completed the conversion of its reusable water bottle manufacturing process to Eastman's Tritan Renew.
announced that as of January this year, it had completed conversion of its manufacturing process for reusable bottles to Eastman’s Tritan Renew, a certified 50% recycled material by the mass balance method of determination.
Widely used to describe recycled content, the mass balance method involves tracking the amount of recycled material entering and leaving the production process and using these figures to calculate the average recycled content in the product.
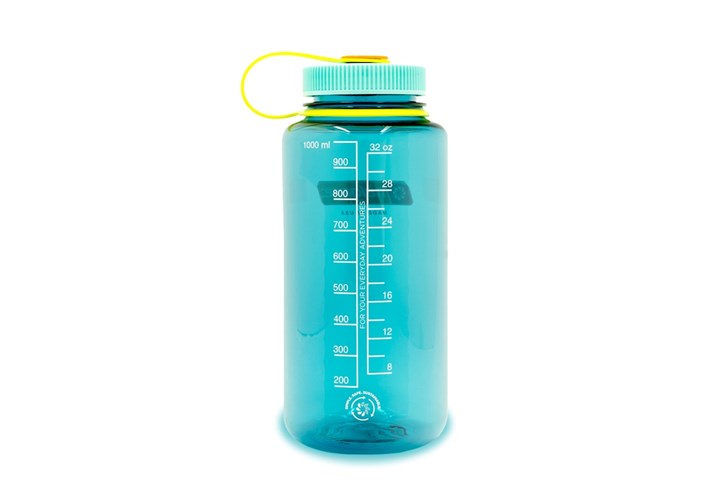
Nalgene reusable water container.
Photo Credit: Nalgene
The reusable bottles made with recycled material are expected to both replace single use bottles and help divert waste plastics from landfills. The process of converting to Tritan Renew, a copolyester, began in 2020. According to the company, it has re-purposed more than 2.35 million pounds of plastic waste since that time, and anticipates using 1.5 million pounds of recycled material each year now that the conversion is complete.
Nalgene bottles have been made using Tritan since 2008, when many brands switched away from using polycarbonate over public
Nalgene Outdoor is based in Rochester, NY and owned by Thermo Fisher Scientific. The company sources and makes its bottles within the United States.
Related Content
-
Avantium and SCGC Partner to Scale-Up CO2- Based Polymers to Pilot Plant
SCGC will use Avantium’s Volta Technology which uses electrochemistry to convert CO2 to chemical building blocks such as glycolic acid which combined with lactic acid make carbon-negative PLGA.
-
CJ Biomaterials Hires Leah Ford as Director of Marketing
Ford has background in biopolymer technology having worked for PLA bioplastics supplier NatureWorks.
-
How to Optimize Injection Molding of PHA and PHA/PLA Blends
Here are processing guidelines aimed at both getting the PHA resin into the process without degrading it, and reducing residence time at melt temperatures.