Multimaterial 3D Printer Developed For Creating Flexible Devices
New printer uses lasers to create graphene, enabling construction of flexible electronic devices.
Scientists have developed a new 3D printer that uses multi-wavelength lasers to create a highly porus graphene from polyimide and graphene oxide. The resulting structure is lightweight, conductive, and can be applied to flexible substrates such as plastics, enabling flexible devices.
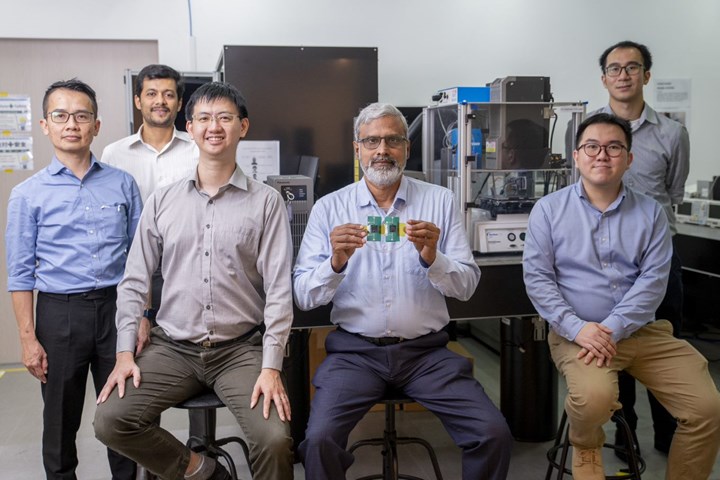
L-R Dr. Low Mun JI, Dr. Suchand Sandeep, Dr. Nicholas Tam, Dr. Murukeshan Vadakke Matham, Dr. Joel Lim, and Daryl Lim. The printer is in the background, and Dr. Matham is holding a sample of a 3D printed pressure sensor. Photo Credit: NTU Singapore
The research is being conducted by scientists from Nanyang Technological University in Singapore, Panasonic Factory Solutions Asia Pacific, and the Singapore Center for 3D printing.
The manufacturer has shown interest in the new printer. The company aims to integrate 3D printed graphene electronics into a smart infusion system. A printed sensor embedded in an IV fluid bag would monitor the status of the IV drip, enabling the system to regulate pressure flow and temperature and transmit information to medical personnel.
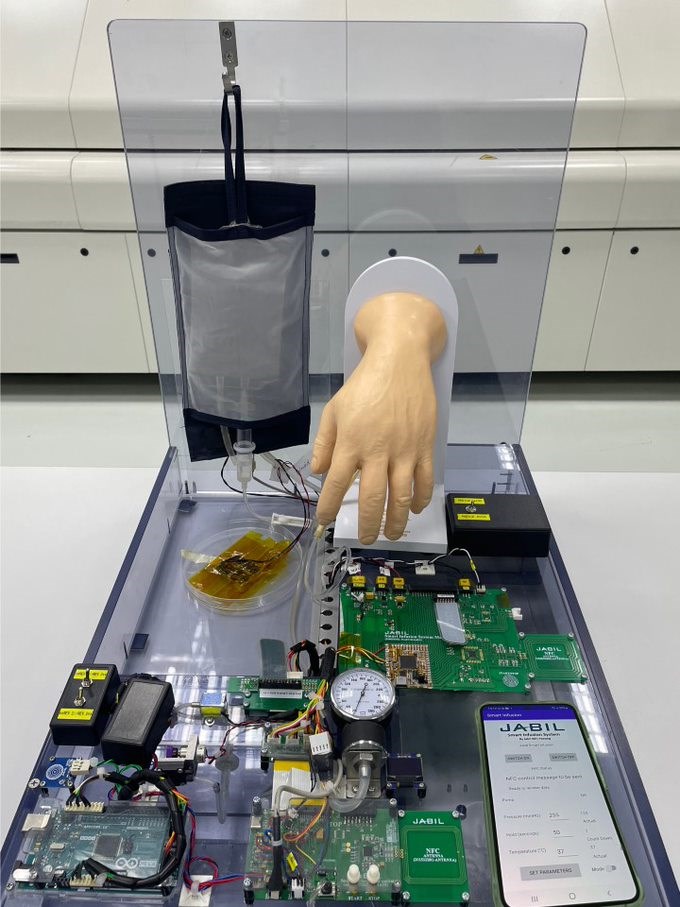
Proof of concept prototype for the smart IV bag system.
Photo Credit: Jabil-MTI Penang
The research team has also tested the possibility of integrating 3D printed components into the fabrication of electronics such as pressure sensors and heaters. The NTU-Panasonic team believes that the newly created 3D printer offers a level of flexibility and functionality unmatched by other similar products in the market. The project members said the innovation has the potential to revolutionise the field of 3D printing and open new possibilities for new product design and innovation.
The collaboration between NTU and Panasonic to develop the new multi-material printer began in 2016. Panasonic has set up a new facility for laser-based manufacturing systems at its research hub in Singapore, which will enable further trials of concepts using components fabricated by the multi-material printer.
Related Content
-
Daimler, OMIC Evaluate Wire-Fed DED for Moldmaking
3D printing a core and cavity on machine from Gefertec, followed by machining, allowed for a complete mold tool to be produced in three days.
-
KraussMaffei Nears Completion of Corporate Headquarters Move
The 185-yr old German maker of plastics processing machinery is shifting to a more than 200,000-m2 greenfield site in Parsdorf.
-
Smooth Operators: Vibration Compensation Improves Robot Performance
Ulendo is working to apply its vibration compensation algorithm to robots. This application is more complex than its initial market of fused filament fabrication 3D printers, but could result in faster, cheaper robots.