MGS Acquires Winther Mould Technology
MGS builds its global footprint with addition of Danish health care tooling manufacturer.
Molder, moldmaker and automation provider MGS, Germantown, Wisconsin, has acquired Danish health care tooling manufacturer Winther Mould Technology A/S. In 大象传媒 for 56 years, Winther Mould is focused on designing, producing and servicing tools for health care clients, and its facility has a dedicated space for sampling, process development and short production runs. An MGS spokesperson told Plastics Technology that the acquisition includes 4,000 m2 (43,000 ft2) of production space and the aforementioned 3,000-m2 (32,000-ft2) test and validation center.
MGS now has 1,200 employees at 12 locations across the U.S., Mexico, Ireland, Denmark, Sweden and Germany. Founded in 1967, Winther Moulds’ new product development operations include design for manufacture (DFM), 3D printing of prototype molds and manufacture of high-volume production tools. As part of its complete mold/machine process validation, the company has proven out new tools and processes on customer machines running in its facility. Starting in 2018, it has sourced all its electricity from carbon-neutral windmills.
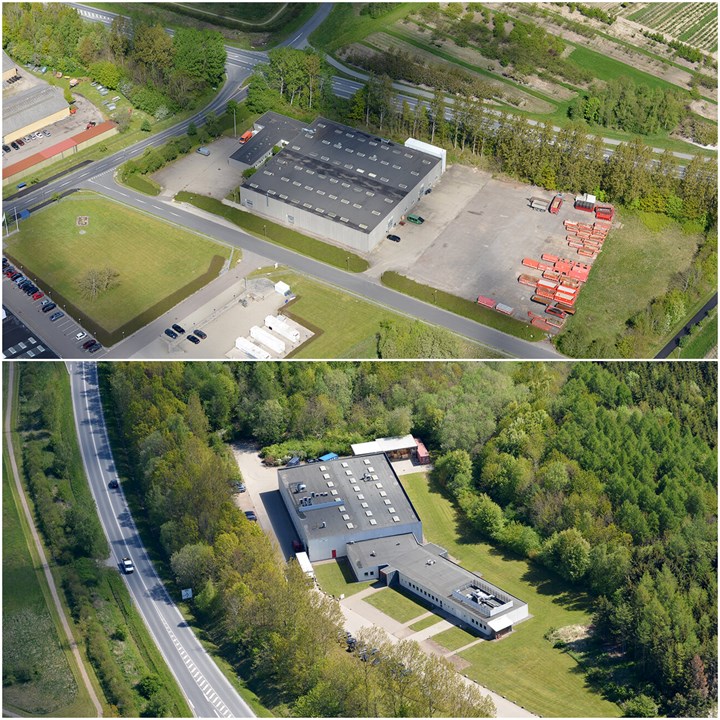
MGS’ acquisition of Danish health care tooling manufacturer Winther Mould includes two facilities. Photo Credit: MGS
Related Content
-
Catheter Specialist Finds Sweet Spot Serving Small, Medium-Sized Concerns
Medical-component specialist LightningCath has carved a niche meeting the needs of small to medium-sized entrepreneurs with complex catheter designs … quickly.
-
What to Look for in High-Speed Automation for Pipette Production
Automation is a must-have for molders of pipettes. Make sure your supplier provides assurances of throughput and output, manpower utilization, floor space consumption and payback period.
-
Medical Tubing: Use Simulation to Troubleshoot, Optimize Processing & Dies
Extrusion simulations can be useful in anticipating issues and running “what-if” scenarios to size extruders and design dies for extrusion projects. It should be used at early stages of any project to avoid trial and error and remaking tooling.