Melt Temperature Measurement Technology Acquired
MTMS has acquired all the rights for the patented plastic melt temperature measurement system for injection molding from Schmit Prototypes.
Newly formed , Janesville, Wisconsin, has acquired the melt temperature measurement technology developed and patented by Richard Bleck from on-demand parts and prototype manufacturer , Menomonie, Wisconsin. Bleck has more than 50 years of experience in injection molding, including 38 years at Phillips Medisize and the former Phillips Plastics. Bleck applied that experience to solve what has always been a nettlesome problem for molders, determining the true temperature of the plastic melt.
In 2020, Bleck’s company, Procon Training and Consulting LLC, Phillips, Wisconsin, was awarded a patent for his solution which utilizes an insulated purge cup to keep the purge molten and then measure its temperature with a thermocouple positioned in the flow path.
After developing and patenting the melt temperature measurement kit, Bleck worked with Schmit Prototypes to produce some of the components for the kit, before eventually partnering with them to manage the sales of the technology.
MTMS says that Schmit’s expertise in precision manufacturing will continue to be utilized moving forward, as will the expertise of Bleck. “MTMS saw how the plastic melt temperature measurement system is far superior to current methodologies, so it was a no-brainer becoming a part of this technology and to advance the utilization of this technology into the injection molding industry,” says Nick LaBansky, MTMS president.
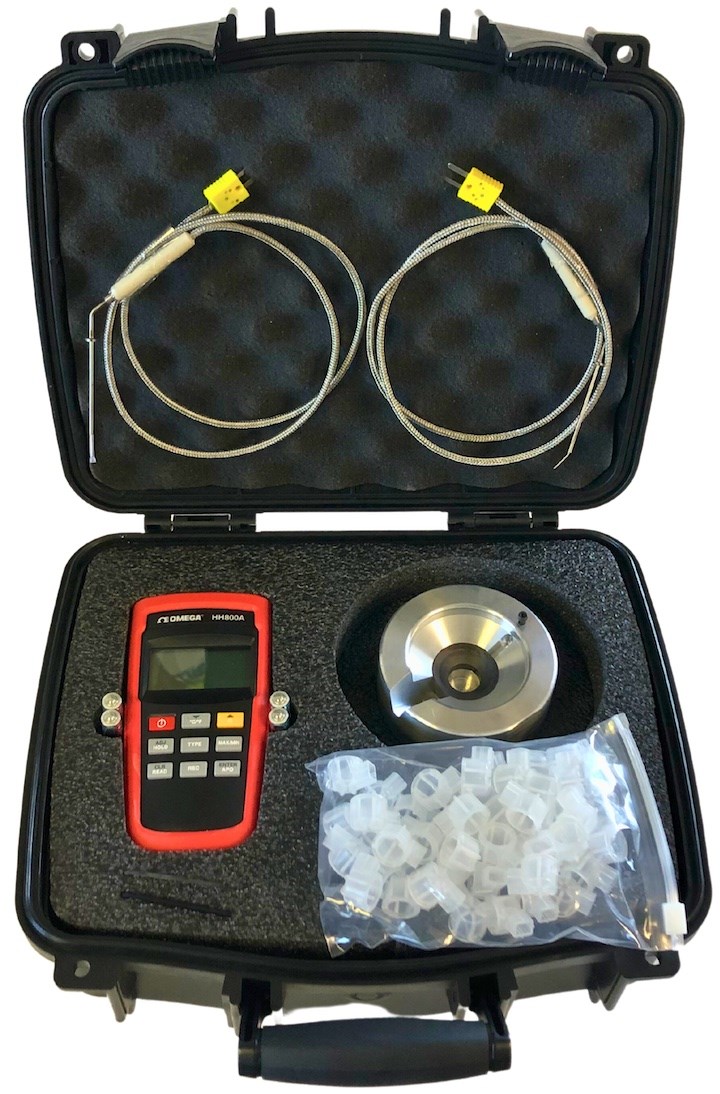
MTMS has acquired the rights to the melt temperature measurement system from Schmit Prototypes. Photo Credit: MTMS
Related Content
-
Hot Runners: How to Maintain Heaters, Thermocouples, and Controls
I conclude this three-part examination of real-world problems and solutions involving hot runners by focusing on heaters, thermocouples, and controls. Part 3 of 3.
-
Process Monitoring or Production Monitoring — Why Not Both?
Molders looking to both monitor an injection molding process effectively and manage production can definitely do both with tools available today, but the question is how best to tackle these twin challenges.
-
Is There a More Accurate Means to Calculate Tonnage?
Molders have long used the projected area of the parts and runner to guesstimate how much tonnage is required to mold a part without flash, but there’s a more precise methodology.