Medical Murray Expands Facilities in Illinois
The medical contract manufacturer added cleanrooms, a testing lab and injection molding space between sites in North Barrington and Lake Zurich.
Medical device design and contract manufacturing firm Medical Murray (North Barrington, Ill.) added a 5200-ft2 dedicated lab to its headquarters and R&D facility in North Barrington, plus a 1600-ft2 Class 7 cleanroom in Lake Zurich, including new injection molding machines.
The new dedicated lab in North Barrington will test devices to ISO and ASTM standards, while also allowing the company to expand prototyping capacity. In a release, Tanner Hargens, Medical Murray’s VP of 大象传媒 development, said the addition gives the company’s engineers full access to a new ISO/IEC 17025 certified testing lab for development and research purposes.
In the 45,000-ft2 Lake Zurich manufacturing facility, the 1600-ft2 Class Class 7 cleanroom adds new injection molding machines, as well as expanded storage and workspace. Medical Murray notes that these additions come a little over a year after the opening of a 30,000-ft2 R&D and manufacturing space in Charlotte, N.C. Between the three facilities, the company now occupies a total area of 85,000-ft2. All three facilities are ISO 13485:2016 certified and FDA registered.
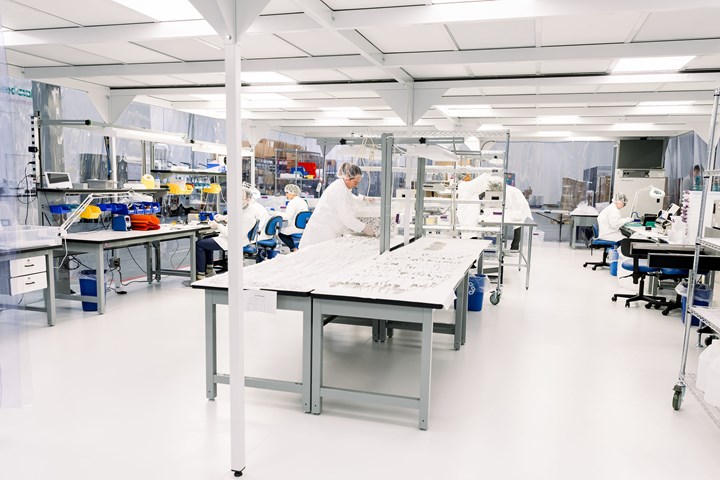
Medical Murray’s latest expansion includes a Class 7 cleanroom at its Lake Zurich, Ill. facility.
Related Content
-
Medical Molder, Moldmaker Embraces Continuous Improvement
True to the adjective in its name, Dynamic Group has been characterized by constant change, activity and progress over its nearly five decades as a medical molder and moldmaker.
-
3D Printed Spine Implants Made From PEEK Now in Production
Medical device manufacturer Curiteva is producing two families of spinal implants using a proprietary process for 3D printing porous polyether ether ketone (PEEK).
-
PHA Compound Molded into “World’s First” Biodegradable Bottle Closures
Beyond Plastic and partners have created a certified biodegradable PHA compound that can be injection molded into 38-mm closures in a sub 6-second cycle from a multicavity hot runner tool.