Manufacturability Analysis for 3D Printing Designs
Protolabs has added a design for additive manufacturability (DfAM) analysis for 3D-printed parts to its online quoting platform, allowing users to optimize designs prior to printing.
Protolabs (Minneapolis, Minn.) has launched instant design for additive manufacturability (DfAM) analysis on 3D-printed parts through its online quoting platform, automating design feedback. Protolabs said DfAM analysis is available globally on parts uploaded to its design portal for any of its plastic and metal 3D printing services. With this technology, customers’ 3D CAD files are put through a digital twin of the selected manufacturing process, identifying key DfAM issues before a part goes to the printer. When users receive their quotes, the analysis highlights potential manufacturability issues for things like thin walls, small gaps or prints that exceed maximum available build size.
Protolabs also announced that it has broadened its additive material and finishing options. Users can choose 3D-printed silicone in multiple levels of shore-A hardness. In addition, vapor smoothing was launched for select materials, providing enhanced finishes that eliminate rough surfaces and leave a glossy, aesthetic appearance on 3D-printed parts. The company already offered automated manufacturability analysis on injection molded and machined parts.
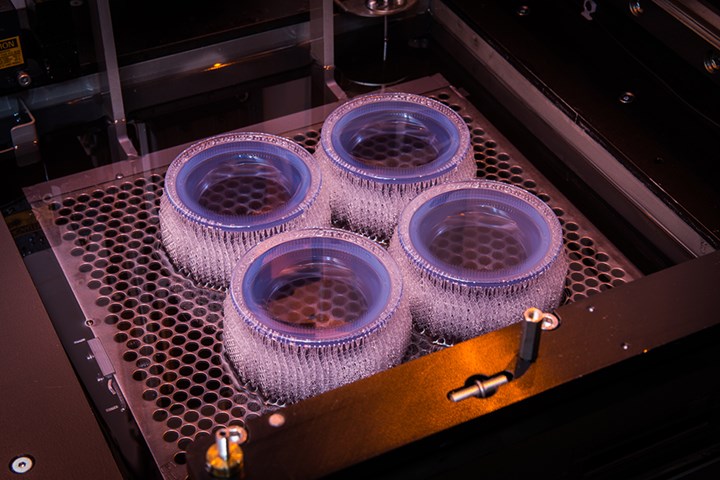
Protolabs says its design for additive manufacturability (DfAM) tool analyzes a 3D print design for any potential issues that could impact its fabrication.
Photo Credit: Protolabs
Related Content
-
The Connector Conundrum: 3D Printed Mold Tooling’s Role in Innovation
ReelView Fishing faced an electronics obstacle in the development of its new technology for underwater video. Additive manufacturing for moldmaking allowed for the speed necessary to iterate to a solution. How inventors and invention will benefit from new ways of obtaining production-ready tooling.
-
KraussMaffei Nears Completion of Corporate Headquarters Move
The 185-yr old German maker of plastics processing machinery is shifting to a more than 200,000-m2 greenfield site in Parsdorf.
-
Additive Fusion Technology Optimizes Composite Structures for Demanding Applications
9T Labs continues to enhance the efficiency of its technology, which produces composite parts with intentionally oriented fibers.