420 Stainless Steel Now Qualified With TrueShape 3D Printing Technology
NPE2024: Mantle's additive manufacturing technology is designed for precision tooling.
Mantle has announced the availability of 420 Stainless Steel for use with its TrueShape 3D printing technology for precision tooling. No hardware modifications or additional components will be required for use with the company’s . The 420 Stainless Steel will be available in the second half of 2024 and will require only an over-the-air software update.
The TrueShape 3D technology, which incorporates fused deposition modeling and CNC machining, enables rapid toolmaking with reduced or even, in some cases, no postprocessing. The process begins with a metal paste which is added in layers. Periodic drying and CNC steps build up the shape of the tool, which is ultimately transferred to an oven for sintering.
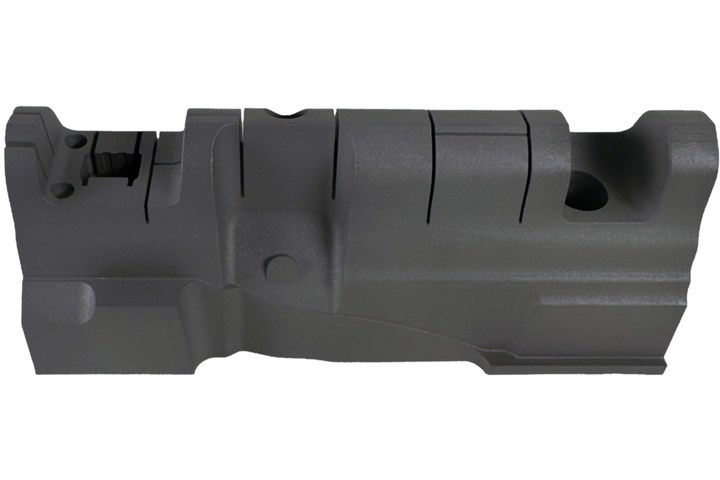
An injection mold insert printed in Mantle’s 420 Stainless Steel. Source: Mantle
According to Mantle, the pursuit of the new material was driven by customer requests. TrueShape 3D was launched with P20 steel, with the later addition of harder H13 steel. The new material will offer similar hardness to the H13, adding superior corrosion resistance.
The availability of stainless is expected to be beneficial to customers in corrosive environments, such as manufacturing locations in tropical climates. “A lot of molding takes place in warm environments, such as Florida, Puerto Rico and Central America, especially for medical. And being able to exist in an environment like that, often requires a noncorrosive steel,” says Paul DiLaura, chief commercial officer at Mantle.
Corrosion is particularly of concern with conformal cooling channels, enabled by additive manufacturing technologies, which offer more efficient cooling than linear channels, thus enabling faster cycle times. “Conformal cooling can lead to a better outcome from a molding perspective, but there’s greater risk and perception of risk of those channels getting corroded or clogged if they rust over time,” DiLaura says. “So having a stainless steel for conformal cooling is perceived as a real advantage.”
At NPE 2024, Mantle plans to display examples of printed steel tooling from the Trueshape 3D technology, along with the metal paste the process begins with, setting up a stark comparison: from a mixture of metal particles, adhesive and solvent that is described as having the consistency of toothpaste, to a dense, heavy, stainless-steel tool ready for industrial injection molding.
Related Content
-
The Connector Conundrum: 3D Printed Mold Tooling’s Role in Innovation
ReelView Fishing faced an electronics obstacle in the development of its new technology for underwater video. Additive manufacturing for moldmaking allowed for the speed necessary to iterate to a solution. How inventors and invention will benefit from new ways of obtaining production-ready tooling.
-
How 3D Printing Supports Toolmaking Workforce at This Multiscale Molder
At more than a century old, General Pattern has seen multiple evolutions in its 大象传媒 — the latest of which is the embrace of additive manufacturing technologies for mold tooling and beyond.
-
5 Trends in 3D Printed Injection Mold Tooling
3D printing has moved beyond conformal cooling, and is now being applied to injection molds more broadly. Observations on additively manufactured mold tooling from the Plastics Technology Expo — PTXPO 2025.