Long Distance Food Packaging Bag Eliminates Metal to Facilitate Recycling
Aran Group's Premium Flex 2.0 eliminates metalized layer while preventing cracking.
announced the launch of the second-generation Bag-In-Box (BIB) Premium Flex 2.0, the successor to the Premium Flex BIB.
In early 2021, Aran Group introduced Premium Flex BIB, engineered to prevent flex crack, an issue frequently encountered in long-distance liquid food transportation. By preventing cracking, the product enabled much greater logistical distances, according to the company.
Building on the success of this predecessor product, Aran Group is planning to launch, in the beginning of 2024, the Premium Flex 2.0, a fully recyclable solution for long-distance transportation of liquid foods.
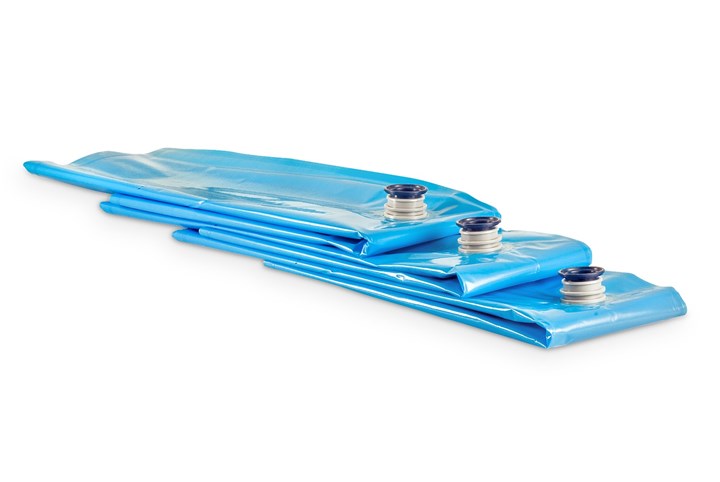
Aran announced a solution for long distance transport of liquid food items, relying on a layer of EVOH with no metal layer. Photo Credit: Aran Group
The most significant innovation in the Premium Flex 2.0 is the elimination of metalized layers. This high barrier packaging solution relies solely on a thin layer of ethylene vinyl alcohol (EVOH) for the barrier, less than 5%, with other layers composed of various polyethylenes. From a recycling perspective, this makes it effectively a monomaterial packaging that can be fully recycled in a PE recycling stream. It supports logistical transport according to the internal lab test distances of up to 8,000 km (4,971 miles), whether by sea, land or air, compared with other bags that allow only 2,000 km (1243 miles).
Traditional solutions for preventing flex cracks require additional materials and packaging operations to fill the empty space in the barrels. However, those solutions do not completely solve the problem. Moreover, the extra packaging materials, such as foamed PS, carry other disadvantages.
Premium Flex 2.0 addresses this challenge, eliminating the need for extra packaging and reducing waste. Weighing less than 500 grams per 220-liter bag and composed of four distinct layers, Premium Flex 2.0 offers a composition that ensures flexibility and durability for the entire package.
Related Content
-
Impacts of Auto’s Switch to Sustainability
Of all the trends you can see at NPE2024, this one is BIG. Not only is the auto industry transitioning to electrification but there are concerted efforts to modify the materials used, especially polymers, for interior applications.
-
PHA Compound Molded into “World’s First” Biodegradable Bottle Closures
Beyond Plastic and partners have created a certified biodegradable PHA compound that can be injection molded into 38-mm closures in a sub 6-second cycle from a multicavity hot runner tool.
-
How to Extrusion Blow Mold PHA/PLA Blends
You need to pay attention to the inherent characteristics of biopolymers PHA/PLA materials when setting process parameters to realize better and more consistent outcomes.