Logitech Scales-Up Use of Recycled Plastic in Electronic Products
About 65% of mice & keyboards in the company’s largest product portfolio now use post-consumer recycled plastic
Switzerland’s (U.S. office in Newark, Calif.) recently announced that it has exceeded its commitment to incorporate PCR into products, reducing its carbon impact and increasing the circularity of consumer product materials and ingredients. Logitech’s largest products portfolio, has surpassed its 50% commitment made in 2020, with 65% of all mice and keyboard units now including PCR plastic. The company claims that it is the first consumer electronics company to commit to providing detailed carbon impact labeling on product packaging across the entire portfolio.
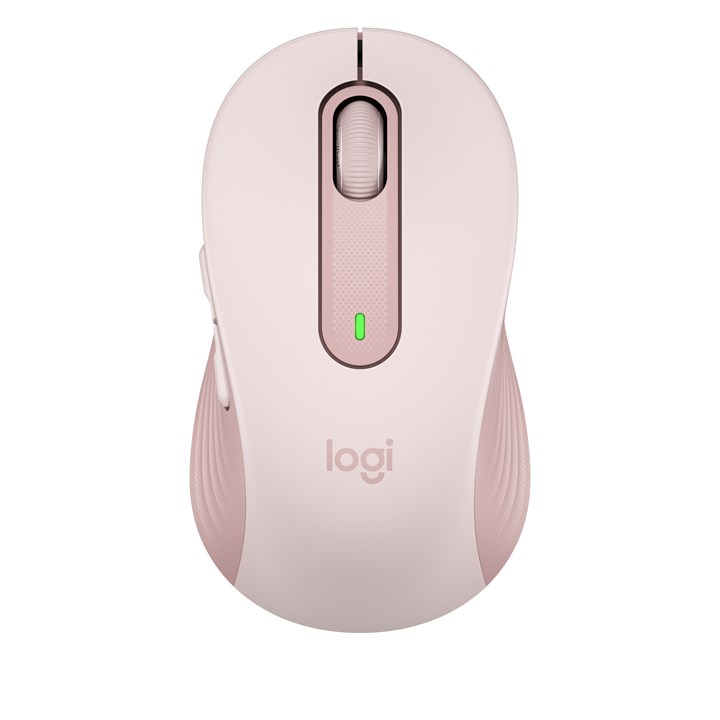
While the company will not share specific details on who they partner with on the production of these programs, they noted that they have been working in partnership for several years with their trusted resin and molding partners to develop and execute these capabilities.
Materials used are ABS and HIPS. Logitech has increasingly used PCR plastic across its product lines as part of its ‘design for sustainability’ approach. Many post-consumer recycled plastic resins have traditionally been limited to black or grey colors and do not typically perform in the same way as virgin plastic. In order to achieve the same level of quality, Logitech innovated on the material characteristics to give these plastics a second life, avoiding the traditional route to landfills. This innovative approach to utilizing second-life materials delivers on the company’s commitment without compromising on the quality and integrity of the material or jeopardizing design aesthetics.
The percentage of recycled plastic in each product varies depending on the type, color, and material make-up of the product and ranges from 75% PCR content to 20% for technically complex lighter color products. As a result of Logitech’s exploration in partnership with trusted suppliers, there are now 30+ colors in the palette and the design goal is to maximize the percentage of recycled content in each product while ensuring high aesthetic appeal and durability tests are met. A few examples of specific products are:
â–ª ERGO M575 Wireless Trackball Mouse is made with 71% PCR plastic in its graphite version, and 21% in its off-white version.
â–ª Signature M650 Wireless Mouse is made with 64% PCR plastic in its graphite version, 26% for off-white and 26% for rose.
â–ª MX Keys Mini is made with 30% PCR plastic in its graphite version, and 12% in its pale gray and rose versions.
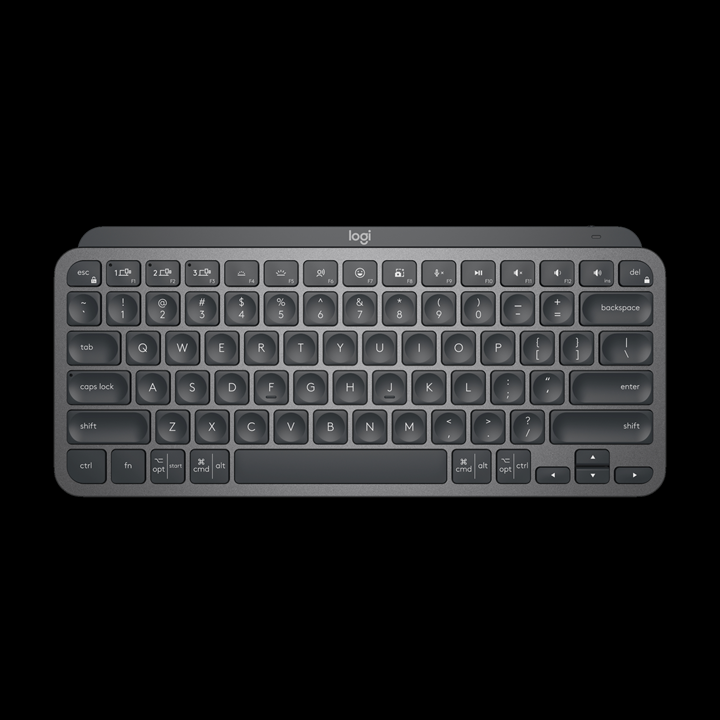
As one of the most used materials in the consumer electronics industry, Logitech is committed to publicly sharing its increasing use of recycled plastic and is taking responsibility for the recovery of e-waste. All of the PCR plastic used in Logitech products comes from end-of-life consumer electronics, which could have otherwise ended up in landfills, and the products are third-party certified through SCS Global Services.
Logitech’s use of recycled plastics has grown rapidly in a mere two years’ time, driving the company to establish new capabilities and further innovate on its design, manufacturing, and sourcing processes. An estimated 17.6 million lbs of virgin plastic was eliminated in Logitech products in 2021, reducing the overall demand for plastic derived from petrochemicals and transforming e-waste into a valuable resource. This equates to an estimated 41.8 million lbs of CO2 saved across the products’ lifecycle, or the equivalent of an average passenger vehicle driving 1,740 times around the Earth.
Said Prakash Arunkundrum, head of global operations and sustainability at Logitech, “We’re taking significant strides to defy ´óÏó´«Ã½-as-usual and deliver breakthrough solutions in materials, packaging advancements, and circularity to lower the company’s carbon impact. Our ultimate ambition is to have a positive impact on the environment and society and drive our whole sector forward by sharing our approach and collaborating.”
Related Content
Automotive Awards Highlight ‘Firsts,’ Emerging Technologies
Annual SPE event recognizes sustainability as a major theme.
Read MoreICIS Launches: Ask ICIS Generative AI Commodities Assistant
Said to be the first of its kind, this AI assistant will enhance access to ICIS’ intelligence and insights for the energy and chemical markets.
Read MoreNPE2024 Materials: Spotlight on Sustainability with Performance
Across the show, sustainability ruled in new materials technology, from polyolefins and engineering resins to biobased materials.
Read MoreAutomotive Awards Highlight Emerging Technologies
Annual SPE Automotive event gives nods to several ‘firsts’ as well as sustainability.
Read MoreRead Next
Beyond Prototypes: 8 Ways the Plastics Industry Is Using 3D Printing
Plastics processors are finding applications for 3D printing around the plant and across the supply chain. Here are 8 examples to look for at NPE2024.
Read MoreFor PLASTICS' CEO Seaholm, NPE to Shine Light on Sustainability Successes
With advocacy, communication and sustainability as three main pillars, Seaholm leads a trade association to NPE that ‘is more active today than we have ever been.’
Read MoreMaking the Circular Economy a Reality
Driven by brand owner demands and new worldwide legislation, the entire supply chain is working toward the shift to circularity, with some evidence the circular economy has already begun.
Read More