Lanxess Develops Concept for Radar Sensors with Integrated Thermal Management
Using its high-performance thermoplastics, Lanxess’ thermal management concept is aimed at autonomous driving.
A new concept for radar sensors with integrated thermal management that will benefit autonomous driving has been developed by Lanxess. While there is still a long way to go, driver assistance systems are increasingly set to become a key feature of future generations of cars, and 360-degree monitoring of the vehicle’s surroundings is enabled by radar waves, among other things.
The radar sensors are an essential component of distance control, lane change monitoring, collision avoidance, and blind spot monitoring systems. As the sensors have to be dust- and water-proof, they are designed as fully-enclosed systems. But this makes it difficult for heat to be effectively dissipated from the inside which can impair the performance of the electronics and durability of the sensors. Said Gregor Jaschkewitz, application developer in Lanxess’ High Performance Materials (HPM), “This is why we developed a concept that allows heat to be dissipated by means of thermally conductive plastics in combination with metallic cooling elements. The individual sensor components are assembled using integrated snap fits and hot rivets, a process that is much less costly and time-consuming than using screws.”
For a radar sensor, Lanxess’ concept involves the following individual components: a front cover (“radome”), radar absorber, printed circuit board (PCB) including antennas, and back cover with an integrated cooling element. The radome faces away from the vehicle and has to be made from a plastic offering a high degree of transmission for the radar waves. PBT is a well suited material here because it has a low dielectric constant (Dk) and loss factor (Df).
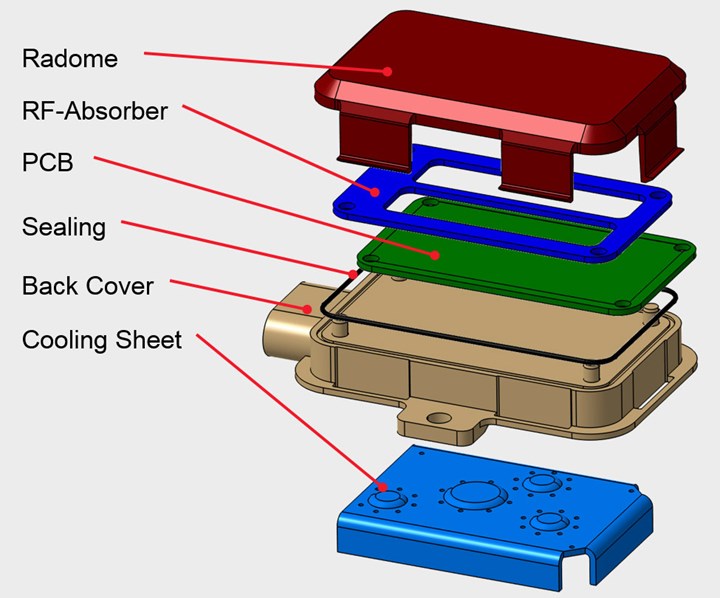
The back cover is the most complex part of the whole assembly. It is manufactured in a plastic-metal compound (hybrid) technique with nylon 6 and a metallic cooling element. This enables engineers to leverage the huge design freedom offered by the injection molding process, allowing them to integrate features such as reinforcement and cooling ribs as well as slots for connectors and the strain-relieved attachment of cables. Most importantly of all, however, the surface of the metallic cooling element can be overmolded with thin areas of plastic. “The heat generated on the electronic components of the PCB can be efficiently dissipated from the whole assembly through these plastic areas. This effect is supported by thermally conductive nylon 6 from our Durethan BTC product range as injection molding material,” says Jaschkewitz. Nylon 6 is also extremely tough and ductile. Another benefit of the hybrid design is that the metallic cooling element shields the electronics inside the radar sensor against electromagnetic radiation, which means that its function is not impaired by external radiation. The assembly can be sealed with O-rings or sealing lips created in a two-component injection molding process.
With most concepts for plastic radar sensors, the radome and back cover have always traditionally been made from thermoplastics that can be welded to each other to create a fully enclosed assembly. This generally meant that the same plastics had to be used for joining.the two components. “Our approach, however, places fewer restrictions on the choice of materials and makes it easier to use tailor-made compounds,” said Jaschkewitz.
Benefiting from the knowhow of a global development partner, Lanxess believes that sensors for driver assistance systems will offer a wealth of opportunities for its Durethan nylons and Pocan polyesters. “We want to benefit from the huge growth potential in this application segment and advance technological innovation with our own ideas – like the concept for radar sensors,” said Dr. Christopher Hoefs, a global application development expert in HPM. For example, the ´óÏó´«Ã½ unit also recently unveiled a concept for the modular design of charging connections for electric vehicles. HPM has pooled its extensive knowhow in material, application, process and technology development under the HiAnt brand in order to support partners and customers in projects. Said Hoefs, “We are supporting our partners at all stages of application development – from concept design, material optimization and mechanical and rheological simulation through to component testing and the start of series production.”
Related Content
Molder Repairs Platen Holes with Threaded Inserts
Automotive molder ITW Deltar Fasteners found new life for the battered bolt holes on its machine platens with a solution that’s designed to last.
Read MoreIndustrial Resin Recycling Diversifies by Looking Beyond Automotive
Recycler equips for new ´óÏó´«Ã½ in medical, housewares and carpeting.
Read MoreGlass Fiber-Reinforced PP With PCR For Automotive
Borcycle GD3600SY will appear in Peugeot vehicles.
Read MoreSkipping the Pellet for Efficient Recycling in Molded Engineering Plastics Applications
AGS Technology leverages deep experience in molding with recycled engineering materials for automotive and heavy equipment parts.
Read MoreRead Next
For PLASTICS' CEO Seaholm, NPE to Shine Light on Sustainability Successes
With advocacy, communication and sustainability as three main pillars, Seaholm leads a trade association to NPE that ‘is more active today than we have ever been.’
Read MorePeople 4.0 – How to Get Buy-In from Your Staff for Industry 4.0 Systems
Implementing a production monitoring system as the foundation of a ‘smart factory’ is about integrating people with new technology as much as it is about integrating machines and computers. Here are tips from a company that has gone through the process.
Read MoreSee Recyclers Close the Loop on Trade Show Production Scrap at NPE2024
A collaboration between show organizer PLASTICS, recycler CPR and size reduction experts WEIMA and Conair recovered and recycled all production scrap at NPE2024.
Read More