Insight Polymers Expands Advanced Compounding Facilities
New twin-screw extrusion line further expands high temperature process capabilities and a configuration of screw elements that enables reactive extrusion.
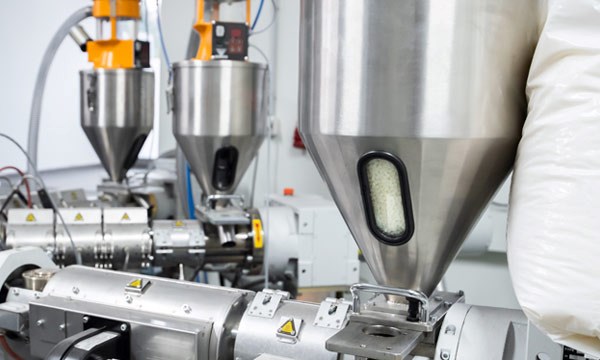
has expanded its advanced compounding facilities in Kingsport, Tenn., with the addition of a new twin-screw extrusion line. The addition further expands capabilities with both high temperature process capabilities and a configuration of screw elements that in addition to conventional compounding enables reactive extrusion processes such as graft polymerization and nanoparticle dispersion and exfoliation. The new capability was developed with Leistritz and represents a modification of the ZSE 40-MAXX platform. Insight Polymers has focused the past several years on a wide range of polymer compounding services including product development, specialty compounding, masterbatches, concentrates, and fully-formulated compounds.
The advanced new line represents a significant investment for Insight Polymer as part of the company’s commitment to advanced polymer processing technology. And the product focus is anticipated to be fully operational in the first quarter of 2023. Founded in 2018, Insight Polymers & Compounding is an independent polymer processing and custom compounding operation in Northeast Tennessee focused on fully formulated systems, product development services and proprietary masterbatches.
Said Insight’s director of operations A.J.Pasquale, “This is an expansion of the specialized services that keeps pace with our customers’ needs in the advanced polymer compounding areas, in particular for additive manufacturing and conductive polymer applications. Added director of innovation Jeremy Lizotte, “This new capability supports our ability not only to extend the range of composite materials with higher concentrations and better dispersion of reinforcements and functional additives, but it also extends our ability to do reactive processing and mechanochemistry which we see as essential to meet new performance criteria.”
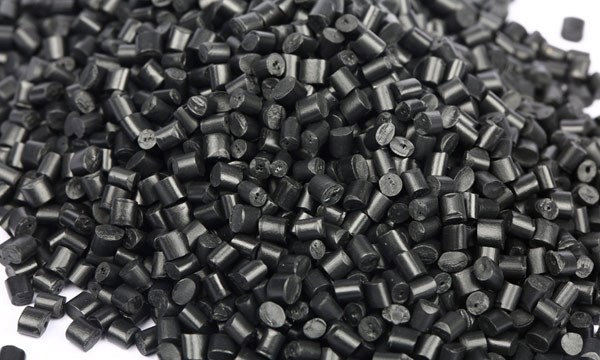
Related Content
-
Let's Take a Journey into the World of Molding Thermosets – Part 1
There are many fundamental differences between thermosets and thermoplastics, from the way raw materials are furnished to the molder and the process in which parts are molded.
-
Polymer Showdown — PC/ABS vs. PC/PBT — May the Best Material Win
First in a series, experts from plastics engineering consultancy The Madison Group will pit leading thermoplastics against each other to see how they differ in processing characteristics, chemical resistance, thermal and mechanical performance, and more.
-
Prices Up for PE, PP, PS, Flat for PVC, PET
Trajectory is generally flat-to-down for all commodity resins.