Freudenberg Medical Adds Six Machines
The Arburg, Wittmann Battenfeld and Toyo machines installed in Baldwin Park, Calif. support component production for in-vitro diagnostic test kits.
Freudenberg Medical (Beverly, Mass.) has added six injection molding machines including three new Arburg molding machines, a workcell for two-shot molding and a Wittmann Battenfeld micro molding machine with in-process visual inspection capability to its thermoplastic molding site in Baldwin Park, Calif.
A company spokesperson told Plastics Technology that the machine additions will boost molding capacity at the site by 10%, with two Toyo machines added along with the Arburg and Wittmann Battenfeld machines. That Wittmann Battenfeld micromolding cell is not the company’s first foray into the technology. The spokesperson noted that Baldwin Park has had micromolding capabilities for several years thanks to an Arburg machine with a micromolding unit. The company didn’t have to to expand its cleanroom footprint to accommodate the new machines.
The new machines range in size from 15 to 110 tons. Added for in-vitro diagnostic test kit component production, the new machines include two-shot processing capabilities that Freudenberg says help streamline manufacturing, reduce SKUs, improve part quality, and reduce costs.
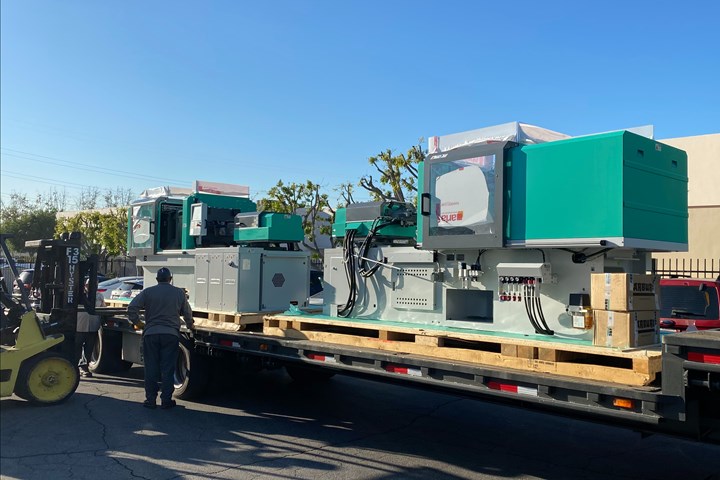
Three new Arburg’s were among the injection molding machines Freudenberg added to its site in Baldwin Park, Calif.
Related Content
-
Hot Runners: How to Maintain Heaters, Thermocouples, and Controls
I conclude this three-part examination of real-world problems and solutions involving hot runners by focusing on heaters, thermocouples, and controls. Part 3 of 3.
-
Optimizing Pack & Hold Times for Hot-Runner & Valve-Gated Molds
Using scientific procedures will help you put an end to all that time-consuming trial and error. Part 1 of 2.
-
Use These 7 Parameters to Unravel the Melt Temperature Mystery
Despite its integral role in a stable process and consistent parts, true melt temperature in injection molding can be an enigma. Learning more about these seven parameters may help you solve the puzzle.