Flexible Film Processor Opens Recycling Lab
TC Transcontinental Packaging’s new facility allows it to facilitate development of new products in the areas of compostable, recyclable, and recycled content packaging.
Flexible packaging specialist has opened its Recycling Technology Lab at the Art, Science and Technology Research and Applications Center (ASTRA Center) in Menasha, Wisc. This lab complements the existing state-of-the-art R&D labs at the Center.
In addition, the ASTRA Center’s Advanced Compost Lab recently received recognition from as a BPI-Approved Lab, allowing TC Transcontinental to serve as a third-party testing lab for those seeking BPI certification or screening for their products.
The 12,200-ft2 ASTRA Center offers the latest technology and deep expertise in compostable, recyclable, and recycled content packaging, enabling increased speed to market from concept to commercialization, optimized solutions for performance and cost, and turnkey packaging solutions. These advances support TC Transcontinental Packaging’s commitment to sustainable packaging practices and producing 100% reusable, recyclable or compostable plastic packaging by 2025.
“As industry leaders in sustainable flexible packaging, we are experts in recycled content, recyclable, and compostable packaging,” notes Alex Hayden, sr. v.p. of TC Transcontinental Packaging’s R&D, Sustainability, and Recycling Group. “The ASTRA Center is at the core of our efforts to drive growth and innovation and be the sustainability partner of choice for our customers. The many tests, instruments, and technologies available to us provide enhanced product development knowledge through the entire process of packaging design to the commercialization of innovative sustainable products.”
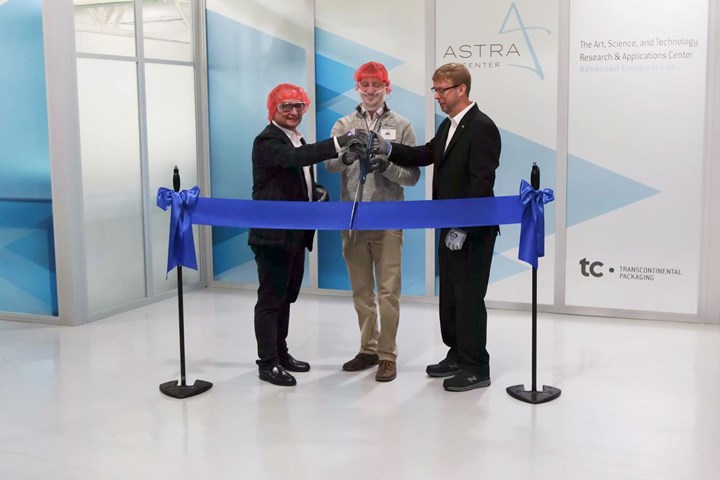
Photo: TC Transcontinental Packaging
The ASTRA Center features:
- State-of-the-art blown film equipment.
- Advanced package testing for the latest recyclability standards, screening new plastic waste sources, and evaluating recycled content.
- Certification of compostable packaging to the latest industrial and home compost standards, as well as capability to quickly and cost effectively screen variables and advance our learnings around new compostable polymers and coatings.
- Physical and analytical laboratories with state-of-the-art equipment to forensically and physically test packaging.
- Latest form, fill, and seal equipment for rapid prototyping and testing of new sustainable packaging developments
The ASTRA Center is comprised of four labs including:
The performs physical testing to simulate real life use of the package from filling to transportation and distribution. It also measures shelf life and consumer end use with analytical testing to develop molecular structures that meet the packaging functionality requirements throughout its entire life cycle.
The is a dedicated lab equipped with a 9-layer blown extrusion line which allows for design experiments and optimization of film formulations. The lab also includes FFS machinery to produce production-scale customer prototypes. This FFS testing is designed to gain insights on how films will perform, avoid any surprises on customers’ equipment, and ensure packaging performance and efficiency once the development stage is completed.
The is the first of its kind within a packaging manufacturer and is fully integrated with the R&D team’s expertise and knowledge to develop the next generation of packaging, and improve the turnaround time and cost for certifying compostable packaging. The lab is accredited, under independent auditing, to conform to ISO 17025 and is equipped to test and meet ASTM D6400 and D6868 standards for compostable packaging.
The includes specialized equipment that takes material through the recycling process from collected film, to compounding and repelletization into recycled resin, to transformation back into film via the lab’s own small-scale blown film line, and optical analysis of the final product. This provides the ability to measure each aspect of a given film structure to ensure it is truly recycling compatible per industry accepted criteria.
Related Content
Multilayer Solutions to Challenges in Blow Molding with PCR
For extrusion blow molders, challenges of price and availability of postconsumer recycled resins can be addressed with a variety of multilayer technologies, which also offer solutions to issues with color, processability, mechanical properties and chemical migration in PCR materials.
Read MoreHow to Extrusion Blow Mold PHA/PLA Blends
You need to pay attention to the inherent characteristics of biopolymers PHA/PLA materials when setting process parameters to realize better and more consistent outcomes.
Read MoreWhat to Look for in High-Speed Automation for Pipette Production
Automation is a must-have for molders of pipettes. Make sure your supplier provides assurances of throughput and output, manpower utilization, floor space consumption and payback period.
Read MorePHA Compound Molded into “World’s First” Biodegradable Bottle Closures
Beyond Plastic and partners have created a certified biodegradable PHA compound that can be injection molded into 38-mm closures in a sub 6-second cycle from a multicavity hot runner tool.
Read MoreRead Next
See Recyclers Close the Loop on Trade Show Production Scrap at NPE2024
A collaboration between show organizer PLASTICS, recycler CPR and size reduction experts WEIMA and Conair recovered and recycled all production scrap at NPE2024.
Read MoreBeyond Prototypes: 8 Ways the Plastics Industry Is Using 3D Printing
Plastics processors are finding applications for 3D printing around the plant and across the supply chain. Here are 8 examples to look for at NPE2024.
Read MorePeople 4.0 – How to Get Buy-In from Your Staff for Industry 4.0 Systems
Implementing a production monitoring system as the foundation of a ‘smart factory’ is about integrating people with new technology as much as it is about integrating machines and computers. Here are tips from a company that has gone through the process.
Read More