Engel Shifts Customer Portal Into a Production Portal, Adds Moldex3D to Simulation Offering
The injection molding machine supplier is utilizing software company TIG, acquired in 2016, to reimagine its e-connect portal and has added Moldex3D to its sim link offering.
Engel’s e-connect customer portal is gradually being extended to a production portal, through the efforts of the machine maker and the software vendor TIG GmbH, which was acquired in 2016 and is now being fully integrated into the Engel group.
Gerhard Dimmler, Engel CTO, laid out the company’s vision during Fakuma 2023. “We want every injection molder to use our e-connect portal as their default start page one day,” Dimmler says, “and we want them to find everything they need for their day-to-day production.” Previewed at K 2022, the strategy expands the previous customer portal into a production portal that will then be compatible with all manufacturers, giving injection molders the ability to map the value-added stages of their production in one place.
Engel acquired software vendor TIG, which developed the authentig MES solution back in 2016. Since then, the distribution of authentig was incorporated into Engel’s Digital Sales department. Engel is now fully integrating TIG’s know-how into its existing structures, merging the software maker into the Engel Group effective Jan. 1, 2024. Engel will absorb all the employees, as well as TIG’s headquarters in Rankweil, Vorarlberg, Austria. Hannes Pils, previously the TIG’s CEO, is now head of service and consulting in Engel Customer Service.
In addition, Engel’s sim link, which exchanges data between process simulations and the injection molding machine, is being expanded and is now also compatible with Moldex3D. Introduced at K 2019, sim link was already compatible with Autodesk’s Moldflow and Simcon’s CADMOULD. Release 1.2 expanded the platform to include the Moldex3D simulation software.
In production, the process settings determined in the simulation are transferred via sim link to the control unit of the injection molding machine as an initial dataset. Then, the process settings, parameters and measurements from the machine, which are optimized during operation, can be stored and fed back into the simulation program. This leads to more accurate data and optimized simulations.
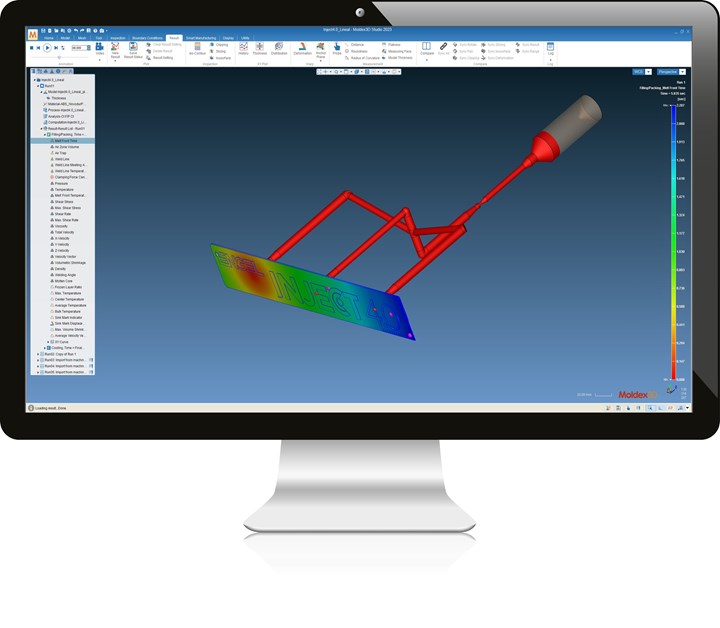
The sim link, which connects simulation to physical production, is now being extended to Moldex3D. Photo Credit: Engel
Related Content
-
Back to Basics on Mold Venting (Part 1)
Here’s what you need to know to improve the quality of your parts and to protect your molds.
-
Process Monitoring or Production Monitoring — Why Not Both?
Molders looking to both monitor an injection molding process effectively and manage production can definitely do both with tools available today, but the question is how best to tackle these twin challenges.
-
Use These 7 Parameters to Unravel the Melt Temperature Mystery
Despite its integral role in a stable process and consistent parts, true melt temperature in injection molding can be an enigma. Learning more about these seven parameters may help you solve the puzzle.