Covestro and Teknor Apex to Cooperate on Compounding TPU
Teknor Apex to market jointly developed TPU compounds with Covestro’s Desmoflex brand.
An agreement to closely cooperate on compounding TPU has been signed by Covestro, Pittsburgh, Penn., and Teknor Apex, Pawtucket, R.I. This extremely versatile plastic has been produced in pure form by Covestro for many years for use in various industry sectors. Through compounding with various other materials and additives, a particular strength of Teknor Apex, the array of achievable properties can be further increased. Covestro is supporting the marketing of the jointly developed products by Teknor Apex with its brand.
New global head of Covestro’s TPU 大象传媒 Thorsten Dreier said, “We are happy to team-up with such a competent and complementary partner for processing TPU on a global scale…Together with Teknor Apex, we want to develop customized products to grow together with our existing and new customers.”
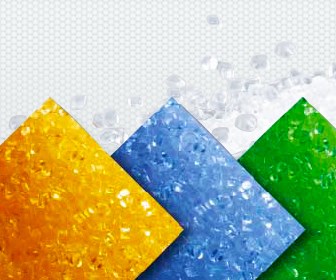
Said Sachin Sakhalkar, v.p. of Teknor Apex’s TPE Division, “We are excited to become Covestro’s preferred global compounding partner. The combination of Covestro’s expertise in TPU resin with Teknor Apex’s custom formulation and compounding capabilities provide a compelling value driver for our combined customers worldwide. This new cooperation strengthens our promise to our customers and partners who depend on us to bring tailored solutions for their application needs.”

Thermoplastic polyurethane (TPU) is used in the automotive industry, in sports and leisure articles, the IT and electronics industry, medical technology and other sectors and can be made with various properties, ranging from soft to hard and from elastic to stiff, depending on customer requirements. All products have in common a high abrasion and wear resistance as well as chemical and weather resistance. The plastic granulate can be processed into profiles, strips, hoses, fibers, films or foams.
Formulating and compounding steps can be used to create an additional value proposition compared to just a neat resin. For instance, specific end-use requirements such as flame retardancy, adhesion, appearance and haptics etc. can be enhanced through specific formulation and compounding techniques.
Related Content
-
What to Look for in High-Speed Automation for Pipette Production
Automation is a must-have for molders of pipettes. Make sure your supplier provides assurances of throughput and output, manpower utilization, floor space consumption and payback period.
-
PHA Compound Molded into “World’s First” Biodegradable Bottle Closures
Beyond Plastic and partners have created a certified biodegradable PHA compound that can be injection molded into 38-mm closures in a sub 6-second cycle from a multicavity hot runner tool.
-
Medical Tubing: Use Simulation to Troubleshoot, Optimize Processing & Dies
Extrusion simulations can be useful in anticipating issues and running “what-if” scenarios to size extruders and design dies for extrusion projects. It should be used at early stages of any project to avoid trial and error and remaking tooling.