Beacon MedTech Solutions Increases Injection Molding Capacity
The company’s Leominster, Mass. facility has recently installed two new Sumitomo (SHI) Demag machines with plans to add an undisclosed number more in the first half of 2022.
Beacon MedTech Solutions has begun expanding the injection molding capacity of the former Acromatic Plastics (Leominster, Mass.), which was acquired by its parent, Beacon Manufacturing Group, in October 2021. Following an initial installation of two SE-EV-A series injection molding machines from Sumitomo (SHI) Demag, Beacon MedTech plans to install an undisclosed number of more presses in the first half of 2022 at the 110,000-ft2 facility.
These machines come standard with direct-drive servo motors on clamp and injection movements, mold parallelism, front flow control (FFC), interchangeable screw and barrels, and simplified integration with automation. Each new machine will include robots, guarding and conveyors.
When Beacon Medtech acquired the Leominster facility in 2021, it announced plans to add cleanroom capacity and build out Beacon’s tooling and liquid silicone rubber (LSR) molding capabilities, enabling the company to support contract manufacturing services of molded products, components and sub-assemblies for single-use applications, Class II Medical Devices, and other medical, bio-pharma, and life science end-use applications.
A company spokesperson told Plastics Technology that Beacon Medtech has a range of thermoplastic and liquid silicone rubber injection molding machines ranging from 30 to 900 tons, with nearly 60 total machines. Formerly Built Rite Reliance & LSR Engineering, Beacon MedTech Solutions is based in Lancaster, Mass.
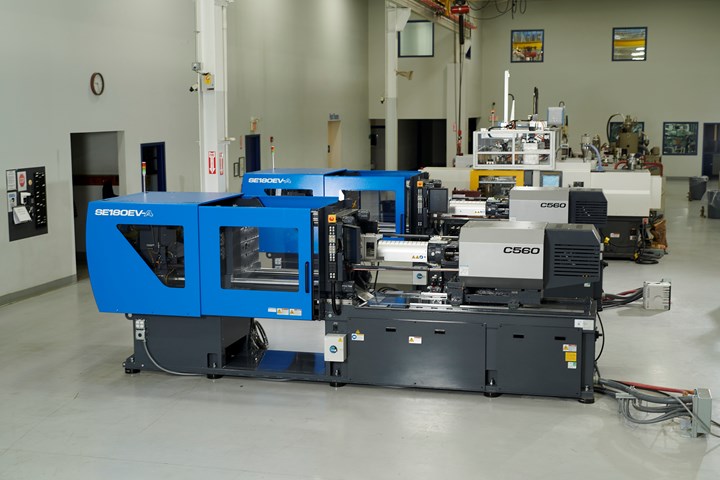
These two, new Sumitomo (SHI) Demag injection molding machines are the first of multiple to be installed at Beacon MedTech Solutions in Leominster, Mass.
Photo Credit: Beacon MedTech Solutions
Related Content
-
For Extrusion and Injection-Blow Molders, Numerous Upgrades in Machines and Services
Uniloy is revising its machinery lines across the board and strengthening after-sales services in tooling maintenance, spare parts and tech service.
-
Get Color Changes Right In Extrusion Blow Molding
Follow these best practices to minimize loss of time, material and labor during color changes in molding containers from bottles to jerrycans. The authors explore what this means for each step of the process, from raw-material infeed to handling and reprocessing tails and trim.
-
Foam-Core Multilayer Blow Molding: How It’s Done
Learn here how to take advantage of new lightweighting and recycle utilization opportunities in consumer packaging, thanks to a collaboration of leaders in microcellular foaming and multilayer head design.