Asahi Kasei Collaborates on Development of High-Quality Recycled Carbon Fiber
Working with academic partners, Asahi Kasei has developed new technology for recycling carbon fiber plastic compounds.
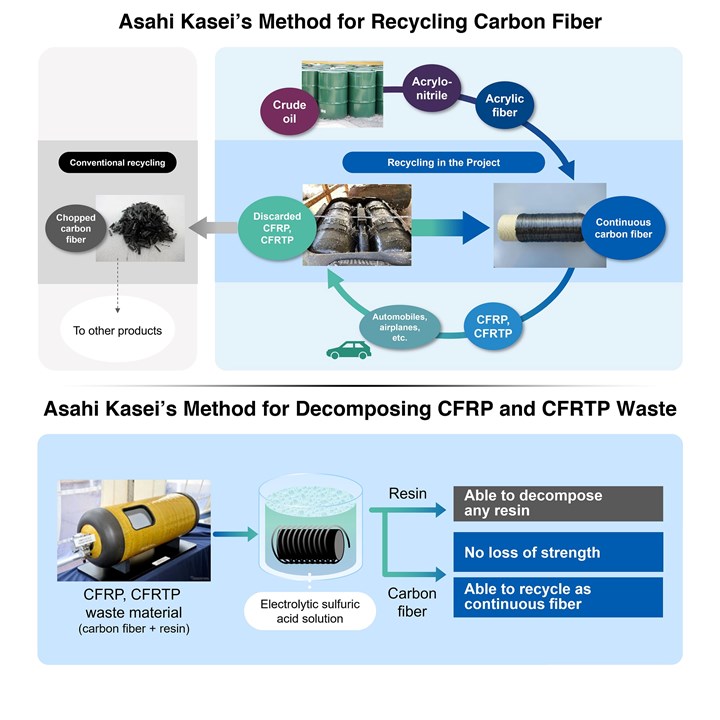
A new technology for recycling carbon fiber plastic compounds has been developed by Asahi Kasei together with the National Institute of Technology at Kitakyushu College and Tokyo University of Science. Carbon fiber reinforced plastics (CFRP) are highly attractive for various industries in demanding application fields due to their unique balance of rigidity, mechanical strength and light weight – also compared with conventional glass fiber reinforced plastics. However, CFRPs are expensive and challenging from a recycling perspective, as it is difficult to extract the carbon fibers from the resin after usage.
In collaboration with its academic partners, Asahi Kasei has developed a recycling method that allows carbon fibers to be extracted from CFRP or carbon fiber reinforced thermoplastics (CFRTP) used in automobiles. This reportedly results in high-quality, inexpensive continuous carbon fiber that can be recycled perpetually, contributing to circular economy. Unlike carbon fiber that is chopped up during the recycling process, Asahi Kasei’s method allows carbon fiber to be extracted from a plastic compound seamlessly, resulting in continuous strands of carbon fiber that can be reapplied in exactly the same manner while retaining properties identical to the original substance.
According to the company, the conventional technologies for recycling carbon fibers by chopping and re-applying them results in a product with lower quality and less durability, insufficient for high-performance applications. To address this issue, Asahi Kasei developed an “electrolyzed sulfuric acid solution method” that allows the carbon fiber to retain its original strength and continuous nature while fully decomposing the resin the carbon fiber is embedded in. This allows for its continued use in high-performance applications and presents an inexpensive, circular solution to the end-of-life dilemma of carbon fiber plastic compounds.
As such, carbon fiber compounds present in vehicles for weight reduction can be easily and inexpensively be broken down at end-of-vehicle-life and reapplied to new vehicles in the future. In addition, Asahi Kasei is developing a carbon fiber reinforced thermoplastic unidirectional tape (CFRTP-UD tape) that utilizes both recycled continuous carbon fiber and the company’s Leona nylon resin. Boasting a higher strength than metal, this CFRTP-UD tape can be applied to automobile frames and bodies, further enabling the recycling of end-of-vehicle-life parts into different, new automobile parts. This is said to present a solution to the long-term challenge that carbon fiber usage for vehicles has posed on the industry and is expected to economically benefit and strengthen carbon fiber’s usage within the automobile industry on a global scale. Moving forward, Asahi Kasei will perform demonstrations and develop the 大象传媒, aiming for practical application around 2030.
Related Content
-
Multilayer Solutions to Challenges in Blow Molding with PCR
For extrusion blow molders, challenges of price and availability of postconsumer recycled resins can be addressed with a variety of multilayer technologies, which also offer solutions to issues with color, processability, mechanical properties and chemical migration in PCR materials.
-
How to Extrusion Blow Mold PHA/PLA Blends
You need to pay attention to the inherent characteristics of biopolymers PHA/PLA materials when setting process parameters to realize better and more consistent outcomes.
-
How to Optimize Injection Molding of PHA and PHA/PLA Blends
Here are processing guidelines aimed at both getting the PHA resin into the process without degrading it, and reducing residence time at melt temperatures.