Arburg Unveils Inline Fiber-Reinforced Additive Manufacturing
At the Hannover Messe 2020, Arburg is producing fiber-reinforced grippers on a Freeformer additive manufacturing machine modified with a feed unit for glass or carbon fibers.
The Freeformer 300-4X at the show features an additional fourth rotation axis and a feed unit for continuous glass or carbon fibers, which are deposited on the part carrier, embedded in a plastic melt and cut to a defined length. With this, Arburg says the process can create parts that are individually and locally reinforced in specific areas as needed. Arburg told Plastics Technology that at the show, the Freeformer will be feeding carbon fibers and the final application will have approximate fiber content of 30 percent. The length of those fibers is theoretically “endless”, according to Arburg, with the size of the part carrier being the only restriction. The company showed a prototype of the Freeformer 300-4X at K2019 for the first time.
Arburg notes that the Freeformer and the Arburg Plastic Freeforming (APF) process is an open system that allows users to optimize process control themselves and run standard plastic pellets. The company says the printed gripper is an example of automation equipment that can be produced on demand in single-unit batches.
At the same event, Arburg showcased its Fiber Direct Compounding (FBC) technology for injection molding. An Allrounder 630 A electric injection molding machine with a clamping force of 250 tons is molding long-fiber reinforced PP carrier plates for car seat adjustment systems. Running a 50-second cycle, the machine is producing parts weighing 330 g with 35 percent fiber content. Arburg told Plastics Technology that the system has proven effective at achieving fiber lengths from 5.6 to 33.6 mm—at Hannover 11.3-mm fibers are produced.
In this system, The FDC unit on the injection unit features a side feeder with an integrated cutting device, as well as an adapted cylinder and a special screw geometry. The glass fibers are supplied as rovings that are cut inline and fed directly into the liquid melt.
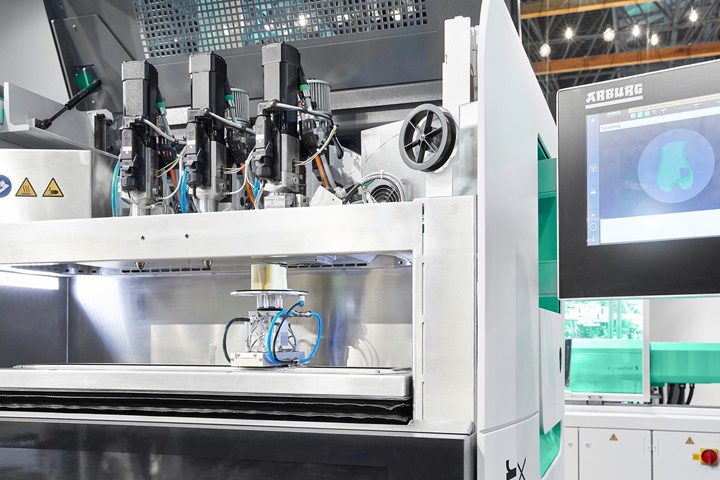
An additional fourth rotation axis and a feed unit for continuous glass or carbon fibers, allows the rovings to be embedded in a plastic melt and cut to a defined length.
Related Content
-
How 3D Printing Supports Toolmaking Workforce at This Multiscale Molder
At more than a century old, General Pattern has seen multiple evolutions in its 大象传媒 — the latest of which is the embrace of additive manufacturing technologies for mold tooling and beyond.
-
NPE 2024: Additive Manufacturing Assisting, Advancing Plastics Processing
Exhibitors and presenters at the plastics show emphasized 3D printing as a complement and aid to more traditional production processes.
-
Additive Technologies for Injection Mold Tooling Ride Tailwinds
NPE2024: Lowering barriers to additive manufacturing adoption in toolmaking.