Agreement Will Bring Commercial Scale Plastic Energy Process to Germany
INEOS and Plastic Energy sign MOU to process 110,000 tons of plastic waste.
and announced the extension of their collaboration around the TAC pyrolysis process, with an agreement to produce 110,000 tons of raw materials from plastic waste at a facility in Koln, Germany. Production is expected to begin in 2026.
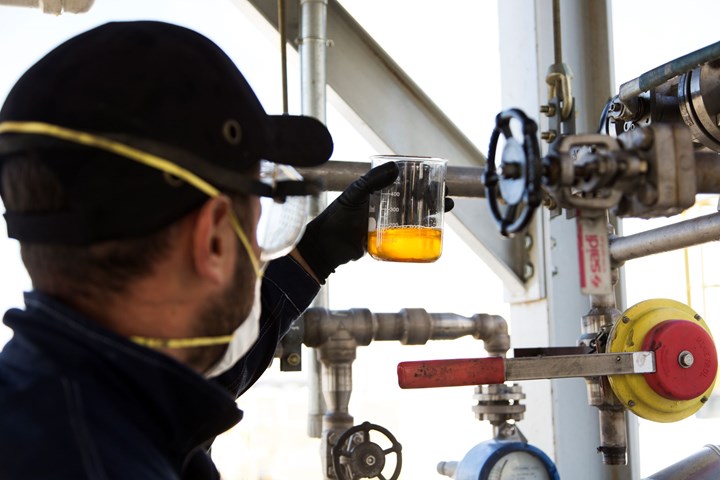
The product of Plastic Energy’s patented process is called TACoil.
Photo Credit: INEOS
Plastic Energy’s TAC (thermal anaerobic conversion) process involves breaking down waste plastics to create an oil, using high energy in an oxygen-free environment. According to a conducted for Plastic Energy by Quantis, the process provides a carbon footprint benefit over virgin production, despite high energy requirements.
The new agreement with INEOS will represent the largest-yet implementation of the TAC process.
INEOS will also invest in technology to process the TACoil further before feeding it to their steam crackers, where it will replace traditional raw materials derived from oil. The products are virgin-quality materials suitable for demanding applications where safety standards require the high levels of product purity and performance.
INEOS and Plastic Energy first announced a collaboration to explore the construction of a commercial scale plant in 2020. TACoil has already been successfully converted into virgin-quality polymer through the INEOS cracker at Köln, Germany, and used by selected customers and brands to demonstrate the viability and demand for materials from advanced recycling.
Related Content
-
Looking to Run More Regrind? PTXPO Workshop Tackles How
When it comes to making injection molding operations more sustainable, the lowest hanging fruit is the use of regrind, but that doesn’t mean it’s not without challenges.
-
Automotive Awards Highlight ‘Firsts,’ Emerging Technologies
Annual SPE event recognizes sustainability as a major theme.
-
PHA Compound Molded into “World’s First” Biodegradable Bottle Closures
Beyond Plastic and partners have created a certified biodegradable PHA compound that can be injection molded into 38-mm closures in a sub 6-second cycle from a multicavity hot runner tool.