The Next 'Big' Thing in 3D Printing
Big Area Additive Manufacturing, or BAAM, is attracting entrepreneurs and machinery developers.
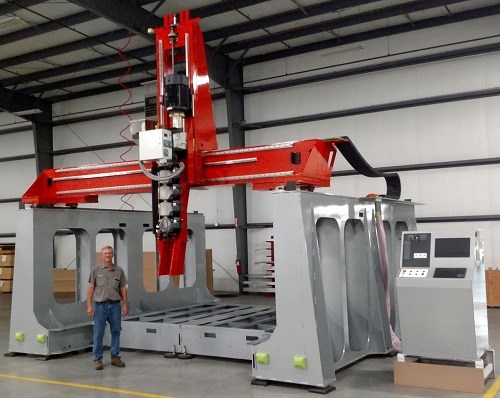
Thermwood's developmental BAAM system with American Kuhne extruder.
Additive manufacturing (AM), better known as 3D printing, is big news these days, and the news in AM is “Big,” as in Big-Area Additive Manufacturing, or BAAM. Visitors to June’s Amerimold exposition in Rosemont, Ill., got an impression of where BAAM is headed. , Oak Ridge, Tenn., showed off examples of its BAAM work at its Manufacturing Demonstration Facility. ORNL made news this past January with its 3D printed Shelby Cobra sports car, which debuted at the North American Auto Show. At Amerimold, ORNL showed an example of its current thrust in making molds for automotive, aerospace, and other composites fabrication. It exhibited a honeycomb section of mold made from ABS with 20% chopped carbon fiber, deposited by an injection molding-type extruder mounted on a CNC gantry in a machine built by Cincinnati, Inc. Capable of dispensing up to 100 lb/hr, it was described as “FDM on steroids” by Dr. Chad Duty, ORNL group leader for deposition science & technology. FDM is fused deposition modeling, an AM method of depositing a hot, continuous filament of thermoplastic in layers to build up a part. In BAAM, the layers can be around 1/8-in. thick.
Duty estimated that a car hood mold could be built in a “couple of hours” and could then be finished with a conventional gel coat. It could then be used for room-temperature cure of epoxy/carbon fiber composites. He said ORNL is working on PPS, PSU, and PEEK tools capable of withstanding elevated-temperature autoclave molding. It has already tested PPS with 40% carbon fiber. At Amerimold, ORNL also showed off a 35-lb chair made in one piece in half an hour from ABS with 20% carbon fiber. It has been load tested to support up to 600 lb.
Besides the Cincinnati machine, ORNL has worked with a six-axis, articulated-arm robot with a material deposition head. Additional options may be available in the near future. For example, CNC router supplier , Dale, Ind., is developing a BAAM machine with a six-axis, gantry-mounted extruder from , Ashaway, R.I. The initial development machine, nearing completion, can make parts up to 10 x 10 ft x 5 ft high. The vertically mounted, 1.75-in. extruder can process over 100 lb/hr. After deposition, a second head on the same machine can machine the part to its final shape.
A second new effort along these lines is a collaborative effort by two firms in Ohio, that are coming at the technology from the extrusion side. Year-old in Youngstown, an extruder builder, is working with of Columbiana, which is supplying special screw, barrel, and check-valve technology derived from injection molding. The goal is to build a vertical, robot-mounted extrusion head that can deposit around 100 lb/hr in a highly controlled fashion. Still in development, the system is designed to ensure highly precise and uniform volumetric deposition of melt as the head moves over a large area at high speed with sudden turns, starts, and stops. The check valve is intended to prevent drool and stringing when deposition stops. The two firms aim to collaborate with a robotics firm to develop a complete BAAM system using a six-axis robot. Expect to hear more on this project in the near future.
Related Content
Daimler, OMIC Evaluate Wire-Fed DED for Moldmaking
3D printing a core and cavity on machine from Gefertec, followed by machining, allowed for a complete mold tool to be produced in three days.
Read More3D Printed Spine Implants Made From PEEK Now in Production
Medical device manufacturer Curiteva is producing two families of spinal implants using a proprietary process for 3D printing porous polyether ether ketone (PEEK).
Read MoreAdditive Technologies for Injection Mold Tooling Ride Tailwinds
NPE2024: Lowering barriers to additive manufacturing adoption in toolmaking.
Read MoreSmooth Operators: Vibration Compensation Improves Robot Performance
Ulendo is working to apply its vibration compensation algorithm to robots. This application is more complex than its initial market of fused filament fabrication 3D printers, but could result in faster, cheaper robots.
Read MoreRead Next
Beyond Prototypes: 8 Ways the Plastics Industry Is Using 3D Printing
Plastics processors are finding applications for 3D printing around the plant and across the supply chain. Here are 8 examples to look for at NPE2024.
Read MoreFor PLASTICS' CEO Seaholm, NPE to Shine Light on Sustainability Successes
With advocacy, communication and sustainability as three main pillars, Seaholm leads a trade association to NPE that ‘is more active today than we have ever been.’
Read More