The 5 M’s of Molding—Part 4: Machine
Match your mold and material to the press to assure that your process control is not limited by poorly functioning machinery.
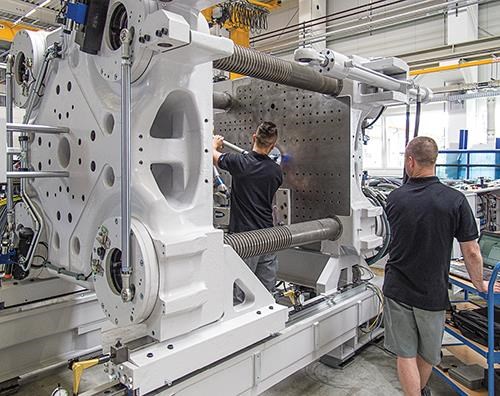
Match your mold and material to the press to assure that your process control is not limited by poorly functioning machinery.
Machinery/Auxilliary Equipment: The molding standard you set is highly dependent upon the machinery and auxiliary equipment you have available to you. Failure to properly assess the capabilities of your equipment will result in a poorly functioning production system. The following components strongly affect a facility’s scrap, downtime and productivity:
- Press: Molding machine capabilities are crucial to the design of any manufacturing system. Press tonnage and screw design (such as general purpose vs. nylon) are key factors in process consistency. Match your mold and material to the press to assure that your process control is not limited due to poorly functioning machinery. Also utilize your process data to further assess process control and machine problems.
- Robot: Robotics systems are a valuable asset for establishing production and quality systems. When evaluating the production system, always review potential fixes through robot improvements, end of arm tooling or programming changes.
- Automation: Other sources of automation should also be reviewed. For instance, if a quality concern keeps repeating itself, look for solutions through automation development. Involve everyone on your production team to fully assess what failures exist within the production system and utilize your engineers to develop working solutions. Better equip your operators and personnel to remove problematic conditions from the production equation.
Preventative maintenance is a key measurable in the Machinery/Equipment category. Unscheduled downtime seriously impedes production efficiencies due to the nature of unexpected system failures and the resulting unprepared approach towards resolution. Scheduled maintenance events are by far the best way to prevent poor performance. Here are some of the areas where preventative maintenance can prevent unscheduled break downs. Each of these components should have their own maintenance log to help establish what concerns are and what frequency of inspection needs to be:
- Molding machine: Press breakdowns can be avoided with a regular inspection system in place. Here are some of the primary inspections and a recommended frequency for performing them:
- Hydraulic Fluid- Quarterly: Fluid samples should be taken and sent to a screener to evaluate metal content and viscosity break down.
- Hoses- Weekly: Inspect hoses for signs of wear, rubbing or blistering.
- Screw- Bi-Annually: Remove screw for inspection. Measure flights and shank to determine whether wear is becoming an issue. Also measure the metering zone of the barrel to verify condition.
- Electrical-Weekly: Look for unsafe conditions and integrity of connectors.
- Heater Bands- Monthly: Verify that all bands are in working condition
- Tooling- It is important to note that a simple 10-minute inspection of every mold per shift can identify problems and prevent hours of down time due to dry slides, pins, etc. Keep detailed records of mold repairs and use them to develop preventative maintenance events and timing. In a short-run shop, simple teardown and cleaning should occur after every run. In cases where molds run for extended periods of time, regular inspection should occur and molds should be torn down and cleaned bi-weekly. In all cases, cleaning frequencies should be developed based on mold history to prevent breakage through intervention and care.
Garrett MacKenzie is the owner and editor of . Mackenzie started in plastics at the age of 19 as an operator, eventually moving up through the ranks to engineering and management over a 29-year timeframe. He currently works as a plastic injection consultant in engineering and training capacities. He can be contacted at garrett.mackenzie@mail.com.
Next week, Part 5 in The Five “Ms” of Molding: Method
Related Content
Three Key Decisions for an Optimal Ejection System
When determining the best ejection option for a tool, molders must consider the ejector’s surface area, location and style.
Read MoreIs There a More Accurate Means to Calculate Tonnage?
Molders have long used the projected area of the parts and runner to guesstimate how much tonnage is required to mold a part without flash, but there’s a more precise methodology.
Read MoreUnderstanding the Effect of Pressure Losses on Injection Molded Parts
The compressibility of plastics as a class of materials means the pressure punched into the machine control and the pressure the melt experiences at the end of fill within the mold will be very different. What does this difference mean for process consistency and part quality?
Read MoreHow to Design Three-Plate Molds, Part 1
There are many things to consider, and paying attention to the details can help avoid machine downtime and higher maintenance costs, and keep the customer happy.
Read MoreRead Next
For PLASTICS' CEO Seaholm, NPE to Shine Light on Sustainability Successes
With advocacy, communication and sustainability as three main pillars, Seaholm leads a trade association to NPE that ‘is more active today than we have ever been.’
Read MoreMaking the Circular Economy a Reality
Driven by brand owner demands and new worldwide legislation, the entire supply chain is working toward the shift to circularity, with some evidence the circular economy has already begun.
Read MoreSee Recyclers Close the Loop on Trade Show Production Scrap at NPE2024
A collaboration between show organizer PLASTICS, recycler CPR and size reduction experts WEIMA and Conair recovered and recycled all production scrap at NPE2024.
Read More