How Smart a Granulator Do You Need?
Some processors see value in grinders that communicate on a network, report preventive-maintenance data, order spare parts, and provide complete maintenance instructions.
I must admit some skepticism when I heard there would be a granulator displayed at the K 2019 show in Germany last October that would have new controls with an unprecedented level of “smart” features and ability to “talk” to other machines or computers over a network, and even order spare parts over the internet. It was billed as bringing the humble scrap grinder into Industry 4.0 or the Internet of Things.
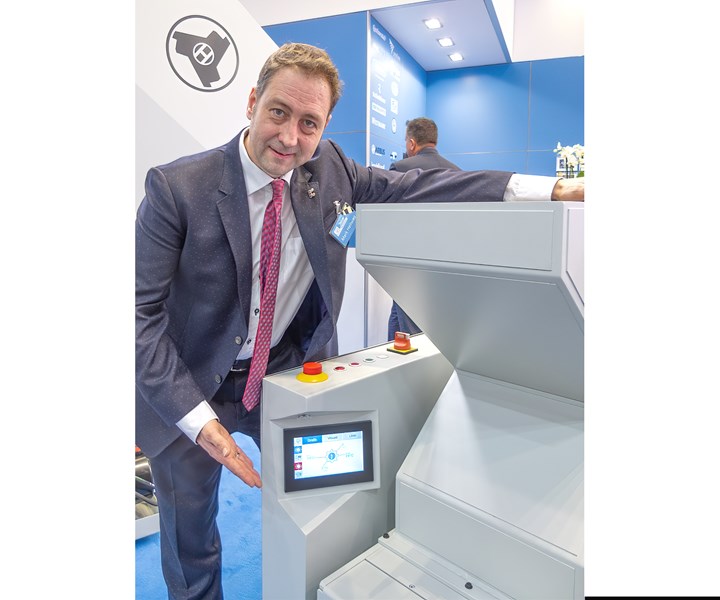
Mark Hellweg, managing director, shows off the new GRANUmaster smart control.
“Who would pay for this?” I thought to myself. “Does anyone really need a ‘talky’ granulator?” And when I asked another supplier of granulators and other auxiliary equipment, that source said that, despite his company’s overall commitment to Industry 4.0, granulators are too price-sensitive a market to support such PhD-level “smarts.”
So I hiked over to the booth of , the German granulator maker, and posed my questions to the first person I could collar. That turned out to be Mark Hellweg, the managing director. I told him that his new controls sounded impressive, but “Is anyone buying them?”. He replied that he had sold a double-digit number of those “smart” models right there at the show. With animated enthusiasm, he proceeded to tell me why.
He started with the ability to program the GRANUmaster smart control touchscreen with specific rpm and torque values for a particular material or part. There’s also an “eco” operating mode, in which the control measures the power consumption over time and “learns” how to apply the optimum settings—worth up to 40% energy savings, according to Hellweg. As noted in the January K Show report on recycling and scrap reclaim by my colleague, Senior Editor Heather Caliendo, users of these new Hellweg machines can select various rotation speeds, so that even very low-melting plastics can be granulated without need for additional cooling. And there’s a “boost” mode to temporarily increase grinding capacity to accommodate fluctuations in demand. This new control is available on all Hellweg granulators from the 2-5 hp, beside-the-press 150 Series on up.
As Heather’s article noted, and Mr. Hellweg was eager to point out, these smart controls record a variety of operating data useful for preventive maintenance: power consumption, rotational speeds, bearing temperatures, and operating hours of bearings, blades, screens and drive belts. This data can be communicated to a central computer via the OPC-UA interface included as standard (the basis of contemporary Industry 4.0 systems). The granulator also can be monitored remotely and can be networked to communicate with upstream and downstream components. What’s more, the granulator controller can be used to issue spare-parts requests and even automatic requests for parts that wear out on a regular basis.
Hellweg also pointed to features such as soft start, safe shutdown (fast stop), V-belt fire monitoring with emergency shutdown, and warning lights when maintenance is required. “I sell safety,” Hellweg stated.
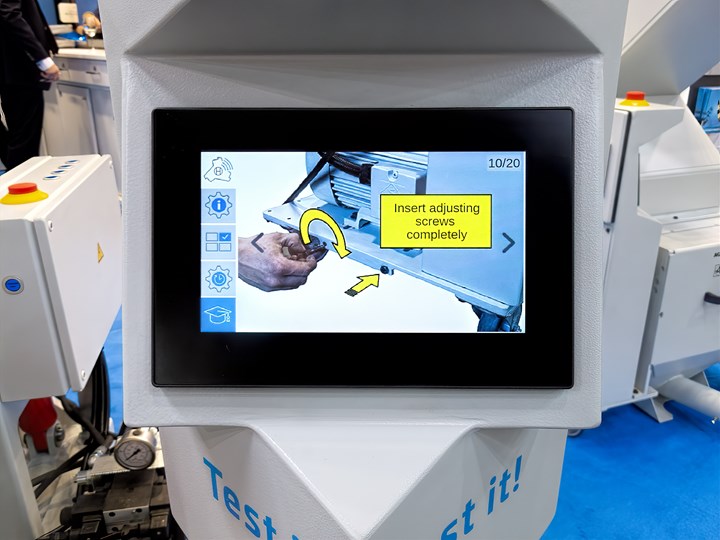
One feature reportedly prized by customers is integration of a full manual into the controls, with step-by-step maintenance instructions.
He was also particularly proud of the inclusion of a complete illustrated manual within the controller, which offers step-by-step instructions for cleaning, blade changing and V-belt maintenance, as well as instructions for general maintenance and visual inspection. Hellweg said this feature definitely contributed to sales of the new controls.
Okay, so maybe everyone doesn’t need a “genius” granulator. But in the coming era of “smart factories,” scrap grinders don’t have to play the dummy, either.
Related Content
Exhibitor Registration Opens for K 2025
Exhibitor registration for the triennial event, which will take place Oct. 8-15, 2025, in Düsseldorf, Germany, is open with a reservation deadline of May 31, 2024.
Read MoreAll-Electric Injection Machines Enable More Sustainable, Energy-Efficient Processing
Stork’s all-electric injection molding machines include a breaking energy feedback system in which recovered energy can be fed back into the customer energy grid.
Read MoreBreaking the Barrier: An Emerging Force in 9-Layer Film Packaging
Hamilton Plastics taps into its 30-plus years of know-how in high-barrier films by bringing novel, custom-engineered, nine-layer structures resulting from the investment in two new lines.
Read MoreWomen in Plastics Event Debuts at K 2025 Oct. 12 in Düsseldorf
The “Women in Plastics” event will debut at K 2025 on Oct. 12 at 4 p.m., where participants will have the opportunity to learn from others’ experiences and build valuable networks.
Read MoreRead Next
Recycling & Scrap Reclaim: Machinery Technology Advances as 'Circular Economy' Takes Hold
The circular economy and recycling were the top themes at K 2019, and machine builders responded with new systems to improve equipment performance and material quality.
Read MoreBeyond Prototypes: 8 Ways the Plastics Industry Is Using 3D Printing
Plastics processors are finding applications for 3D printing around the plant and across the supply chain. Here are 8 examples to look for at NPE2024.
Read MoreMaking the Circular Economy a Reality
Driven by brand owner demands and new worldwide legislation, the entire supply chain is working toward the shift to circularity, with some evidence the circular economy has already begun.
Read More