American Manufacturing Steps Up to the Coronavirus Challenge
Plastics processors are among the manufacturers that stepped up big-time in the face of the global COVID-19 pandemic. I’m proud to turn over this space this month to Rick Kline Jr., president of our parent company Gardner Business Media, whose comments below (edited) appeared originally March 31 in a OpEd piece published by the Wall Street Journal.
As a media provider to the manufacturing industry, my company has borne witness to the front lines of American manufacturing for more than 90 years, where the stories of sacrifice, ingenuity and common purpose are as countless as they are awe inspiring. As I write this, manufacturers of all sizes across the country are coming together to produce complex medical devices such as ventilators and N95 masks, finding creative and efficient ways to manufacture all the components that go into COVID-19 testing kits and countless other products needed in the fight against this new and invisible enemy.
The most amazing thing (and frankly, it’s not at all surprising for those of us who know the people that own, manage and work in these 大象传媒es) is that our government did not need to direct this undertaking. The women and men who constitute America’s manufacturing might are doers. And they are getting it done.
As impressive as the mobilization of American manufacturing has been, the use of technology to get the word out and enable the escalation to take place is even more impressive. From social media to digital design and additive manufacturing (industrial 3D printing)—communications and processes that would have taken weeks or months to transpire are literally happening overnight.
Ford and 3M, for example, have been working together since 1925, when masking tape was invented. Now they’ve taken that to a whole new level as Ford manufacturing engineers are on the factory floor of 3M facilities, helping increase the production of things like ventilators and N95 masks. What’s more, they are partnering on the reengineering of a pure-air respirator so that Ford can use components from its parts bin—like the fan to cool the seat in an F-150—to quickly scale production of these life-saving devices.
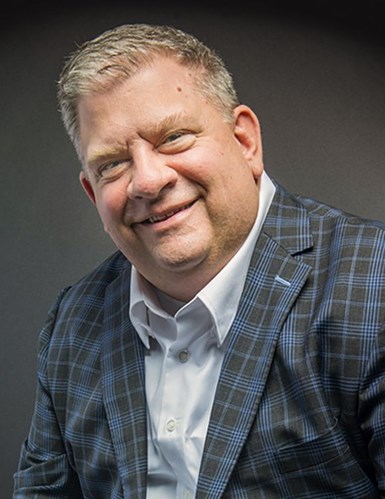
Rick Kline Jr., president of Gardner Business Media, parent company of Plastics Technology and eight other magazines devoted to discrete-parts manufacturing.
3D printer maker Stratasys has committed its own 3D printers and organized the efforts of its customers providing time on their 3D printers toward a shared effort to needed by healthcare workers at a rate of thousands per week, and HP’s 3D R&D centers are collaborating with partners around the world in a coordinated effort to increase production. Initial applications being validated and finalized for industrial production include face masks, face shields, mask adjusters, nasal swabs, hands-free door openers and respirator parts.
The whole world is a better, safer place if we deploy our capabilities closer to the markets being served. Think of it as “Farm to Table Manufacturing.”
General Motors voluntarily entered into a partnership with Washington-based Ventec Life Systems aimed at making GM manufacturing resources available to help Ventec rapidly scale up ventilator production. GM’s commitment was motivated by compassion and concern for the urgent medical need, no doubt, but also driven by the company’s simple recognition that its fortunes and future success rely on the continued health of the people of the country it calls home.
In this time of crisis, we are learning a lot about our ourselves, our neighbors, our country and our world. Hopefully, as the dust settles from these trying times, we learn how critical a strong industrial policy is for our country. We recognize that we all need to be good global citizens. But we must also recognize, as a nation, that we must be self-reliant.
We must have better control of our supply chains, not because we want to be isolationist, but because the whole world is a better, safer place if we deploy our capabilities closer to the markets being served. Think of it as “Farm to Table Manufacturing.”
Despite rumors to the contrary, America is a juggernaut of manufacturing. We are a nation of problem solvers and inventors. And, while we are overcoming today’s crises, we are standing at the precipice of a Renaissance of American Manufacturing.
Our brightest days are right in front of us.
Related Content
Understanding Melting in Single-Screw Extruders
You can better visualize the melting process by “flipping” the observation point so the barrel appears to be turning clockwise around a stationary screw.
Read MoreShredding Thin Film: How to Do It Right
While many processors recoil at this task, a little know-how in shredding equipment, processing, and maintenance should add the necessary confidence.
Read MoreWhat to Know About Your Materials When Choosing a Feeder
Feeder performance is crucial to operating extrusion and compounding lines. And consistent, reliable feeding depends in large part on selecting a feeder compatible with the materials and additives you intend to process. Follow these tips to analyze your feeder requirements.
Read MoreNPE2024 Wrap-Up: Sustainability Dominates Show Floor News
Across all process types, sustainability was a big theme at NPE2024. But there was plenty to see in automation and artificial intelligence as well.
Read MoreRead Next
Lead the Conversation, Change the Conversation
Coverage of single-use plastics can be both misleading and demoralizing. Here are 10 tips for changing the perception of the plastics industry at your company and in your community.
Read MoreFor PLASTICS' CEO Seaholm, NPE to Shine Light on Sustainability Successes
With advocacy, communication and sustainability as three main pillars, Seaholm leads a trade association to NPE that ‘is more active today than we have ever been.’
Read More