Thermoformers running non-servo-eject trim presses will have access to a first-of-its kind automation solution thanks to new technology introduced recently by BMG. Its Mantis Robotic Trim Press Handler was developed by NAS Nalle Automation Systems, a BMG company, and is billed as the industry’s first robotic system that reliably handles the flow of parts ejected from any non-servo trim press, including those made by BMG competitors. The fully automated system reportedly can reduce labor requirements by up to 75%, and the modular robotic design allows for tool changeovers in under an hour. Mantis has been running since March at an undisclosed Midwest thermoformer on a line making PP lids.
Before this innovation, parts ejected from non-servo trim presses had to be manually separated and counted, a labor-intensive, error-prone and inconsistent process that limits the automation of downstream packaging functions. NAS solved this problem with its patent-pending Trim Press Receiver (TPR), which uses a unique separating mechanism to count and contain stacks of product, followed by a raking mechanism to take the product into the receiver for transfer by the robot.

Photo shows various components of the new Mantis Robotic Trim Press Handler. (Photos: BMG)
Kurt Huelsman, president of NAS, calls the TPR the “core of the line.” As he explains, “Being able to cut into the ‘deck of cards’ of multiple lanes of product, separate them, and then contain them as they are pulled off the trim press while it is still running does not sound hard. But no one has ever done it effectively before. Mantis can handle products that have been relegated to non-servo eject because they are hard to handle, such as lids, which don’t nest well. Without the TPR, we have a nice robotic handler. With it, we have a non-servo-eject system that can handle products previously unable to be automated. The future of thermoforming is for automation to be built in, not simply an option or accessory.”
“The future of thermoforming is for automation to be built in, not simply an option or accessory.”
He adds, “Consistent and reliable separation of product on a continuously flowing, non-servo-eject trim press was the key to the development of Mantis. The design of the receiver, coupled with NAS’s robotic automation capabilities, brings a safe, productive and cost-effective solution to a historically very manual process.”
How it Works
As Jon Smalling, director of automation for NAS, explains, the TPR is butted up against the trim press. Raking and separating mechanisms within the TPR collect parts, which are presented to a six-axis robot equipped with product-matching, quick-change end-of-arm tooling (EOAT). The robot automatically transfers product to a Shuttle Station, which, after kicking out mis-trim or off-spec parts, integrates with downstream packaging functions that include wrapping, boxing, case packing, sealing and palletizing. Incorporating the robot allows the Mantis system to be very compact and configurable, making installation possible where floor space is limited or obstructed, BMG says.

Here, the Mantis robot transfers lids from the TPR to the shuttle.
BMG bills Mantis as configurable and adaptable. Explains Huelsman, “First of all, we can work with non-servo eject and servo trim presses from any supplier; the TPR interface designed for a BMG trim press would be different than for other brands. So there will be features to the TPR that will be unique to the particular trim press in terms of fixturing, attachments, etc. Adds Smalling, “The TPR takes up about the same space as operator interaction, if not less. Remember, a typical thermoforming plant has to allot space for three to five humans for pulling, separating and counting stacks of product. Our robot and shuttle station are completely reconfigurable. We’ve designed a system that can ‘dance around’ any existing footprint.”
Introduction of Mantis comes at a time when processors of all kinds are looking for automation solutions to improve efficiencies and mitigate ongoing worker shortages. Notes Bob Gordert, BMG’s v.p. sales for the Americas. “On the post-trim side, a very large percentage of our customers are requiring downstream automation to justify new thermoforming equipment in order to achieve their ROI and to mitigate exposure to workforce shortages.”
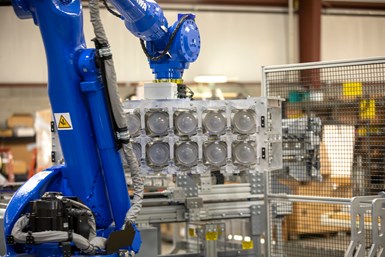
Close-up of Mantis robot with quick-change toll transferring lids that had been separated and stacked in TPR.
“We are excited about the first installation of the Mantis Robotic Trim Press Handler from NAS,” says Paul Phillips, BMG’s v.p. marketing. “The system will help thermoformers keep their lines running despite the labor shortages they are facing. The Mantis offers quick product changeovers and full product containment from the Trim Press to the bagger, all within a compact footprint with minimal human interaction. We fully expect the Mantis to provide themoformers with more uptime and reliable trim-press handling that grows with their 大象传媒.”
“Our robot and shuttle station are completely reconfigurable. We’ve designed a system that can ‘dance around’ any existing footprint.”
Gordert says the partnership with its beta customer made sense because this particular thermoformer was committed to testing the TPR, its connection to the trim press (a non-BMG machine), and its ability to strip, rake and contain the product all the way through the robot tool. The installation went “smoothly, with minimal issues.” Huelsman says Mantis was up and running within two to three days and running around the clock within five days.
Optional features offered with the Mantis include remote monitoring for preventive maintenance, predictive maintenance, cycle-time analysis and other functions.

Mantis EOAT feeding lids to shuttle station.
The BMG Group is made up of Brown, Lyle, GN, Freeman (a supplier of thermoform tooling), NAS, and aXatronics. The latter is a certified Motoman Robotics strategic partner that focuses on creating high-level mechatronics process-engineered solutions for challenging processes in manufacturing. NAS, a 25-yr-old company, was acquired by BMG in 2016.
Related Content
3D Printed Spine Implants Made From PEEK Now in Production
Medical device manufacturer Curiteva is producing two families of spinal implants using a proprietary process for 3D printing porous polyether ether ketone (PEEK).
Read MoreNPE2024 Wrap-Up: Sustainability Dominates Show Floor News
Across all process types, sustainability was a big theme at NPE2024. But there was plenty to see in automation and artificial intelligence as well.
Read MoreNovel Line Turns Fluff to Blown Film
Processor Bioflex of Mexico is utilizing Reifenhäuser Blown Film’s EVO Fusion technology to integrate postindustrial and postconsumer recycled materials into products.
Read MoreImpacts of Auto’s Switch to Sustainability
Of all the trends you can see at NPE2024, this one is BIG. Not only is the auto industry transitioning to electrification but there are concerted efforts to modify the materials used, especially polymers, for interior applications.
Read MoreRead Next
Lead the Conversation, Change the Conversation
Coverage of single-use plastics can be both misleading and demoralizing. Here are 10 tips for changing the perception of the plastics industry at your company and in your community.
Read MoreFor PLASTICS' CEO Seaholm, NPE to Shine Light on Sustainability Successes
With advocacy, communication and sustainability as three main pillars, Seaholm leads a trade association to NPE that ‘is more active today than we have ever been.’
Read MoreBeyond Prototypes: 8 Ways the Plastics Industry Is Using 3D Printing
Plastics processors are finding applications for 3D printing around the plant and across the supply chain. Here are 8 examples to look for at NPE2024.
Read More