Medical Manufacturer Innovates with Additive Manufacturing and Extrusion Technology Hubs
Spectrum Plastics Group offers customers two technology hubs — one for extrusion, the other for additive manufacturing — to help bring ground-breaking products to market faster.
Among medical-device component suppliers, it’s not a stretch to say that precision and innovation come with the territory. But it’s also not a stretch that , a manufacturer of medical tubing, complex catheter delivery systems, injection molded components and flexible packaging, has been on a mission to kick its technical processing capabilities up a notch.
A little more than two years ago, the company launched the Spectrum Innovation & Technology Hubs (SITHs) at its Sandy, Utah site. The idea was to use these hubs to help Spectrum bring new technical solutions to medical-device manufacturers that continually seek more complex products — from thin-wall, tight-tolerance extrusions with multiple lumens, to material combinations previously not thought feasible — faster than ever.
Spectrum has now launched two such hubs in Sandy: one for the continued development of its extrusion 大象传媒, headed up by Matt Bills, sr. v.p. of Extrusion Innovation & Technology; the second for (AM), run by Tyler Stark, sr. dir. of Additive Manufacturing and Innovation. At the AM SITH, 22 machines employing proprietary technology were designed by Stark and built in-house at Spectrum. At the Extrusion SITH, Bills welcomes visitors to the 3000-ft2 wing equipped with full-scale extrusion lines, including a 1-in. line already in place and a 2.5-in. line scheduled for installation.
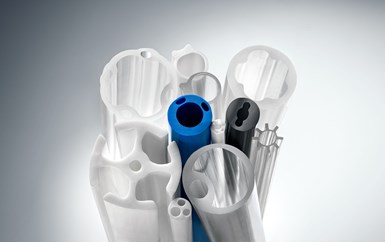
Spectrum Plastic Group’s Extrusion SITH allows the company and its customers to work collaboratively to develop next-generation medical tubing. (Photo: Spectrum Plastics Group)
“When our competitors bring customers on-site, many won't allow them to see the process run,” Bills says. “Many are concerned that the customer will learn what they are doing and take the 大象传媒 from them. On the contrary, we have a dedicated space open to all customers. Why? For one thing, I want our customers to learn as much as possible about extrusion because many times a customer will assume that if SolidWorks can draw it, then we can extrude it. Of course, that’s not always the case, so at the SITH we help educate the customer to the possibilities in real time. Here, the customer doesn’t just see an extrusion line run, but gets a bit of an education at the same time.”
The Extrusion SITH also encourages collaboration between the customer and Spectrum on new ideas — more complex profiles, wider range of durometers, and multiple material combinations, to name a few. “Our customers are always asking us to push the envelope. At the SITH, we’re offering them a way to work with our engineering team in person and on-site while making their extrusions and, more importantly, exchange ideas and make adjustments on the spot.”
As Stark explains, the AM SITH accommodates out-of-the-box ideas customers are bringing to them with greater frequency. He elaborates, “Some of our customers are now using 3D printing to create more complex parts from multiple materials that in the past could not be produced using traditional manufacturing methods. We can do unique things here; we can 3D print extrusion tubing in infinite lengths, and actually have run up to 80-ft long. Just to prove that we could do it, we’ve 3D printed a tube with 78 lumens.”
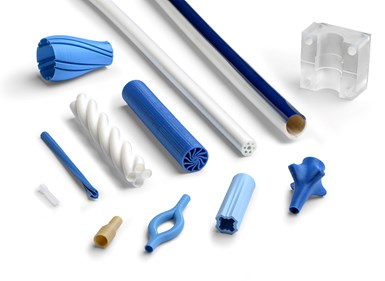
Spectrum has developed and built its own additive manufacturing machines to help customers with both R&D and production requirements.
Why would one want to 3D print a tube? Stark replies, “For one thing, we can sometimes print geometries that you can't really extrude or would have trouble extruding. But more importantly we can satisfy the needs of customers that want to try out different materials, different profile shapes, dimensions and the like. So, in the case of multi-lumen profiles, we can produce these in three to five days without worrying about machining dies and making different tooling iterations. I don't know of anybody else that can do that in the world. But we're also trying to get to our customers to really think outside the box in terms of development; not just producing products using conventional methods, but meeting demand if an application needs two or three different materials in a part or a feature that can't be necessarily molded or extruded.”
As a primary focus, Stark says the AM SITH is currently a great fit for early-stage development within R&D projects to provide prototype samples with the ability to quickly iterate between designs. In addition to using the 3000-ft2 SITH for development programs, at press time Spectrum was finishing a 900-ft2 Class 7 clean room where 3D printers will be making production parts, possibly even for use inside the body. Spectrum’s machines can handle a range of different materials in different forms, including filament supplied by Spectrum’s extrusion lines. Stark notes, “We're across the whole spectrum, no pun intended, from R&D all the way to production as our long-term goal.”
The two hubs work hand-in-hand to solve complex problems. Bills explains: “A customer sometimes comes back to us if they realize they're off in their calculation on, say, flexural modulus. They tell us, ‘We really need this tube in 55 Shore A.’ This is where Tyler can step in and offer to 3D print tubes in various durometers quickly. So, they’ll get a flavor of what they really need, and then we can take it to the production step. This way, we are cutting out time in development, helping them get their product to market faster.”
Related Content
Roll Cooling: Understand the Three Heat-Transfer Processes
Designing cooling rolls is complex, tedious and requires a lot of inputs. Getting it wrong may have a dramatic impact on productivity.
Read MoreShredding Thin Film: How to Do It Right
While many processors recoil at this task, a little know-how in shredding equipment, processing, and maintenance should add the necessary confidence.
Read MoreHow Polymer Melts in Single-Screw Extruders
Understanding how polymer melts in a single-screw extruder could help you optimize your screw design to eliminate defect-causing solid polymer fragments.
Read MoreHow to Select the Right Cooling Stack for Sheet
First, remember there is no universal cooling-roll stack. And be sure to take into account the specific heat of the polymer you are processing.
Read MoreRead Next
See Recyclers Close the Loop on Trade Show Production Scrap at NPE2024
A collaboration between show organizer PLASTICS, recycler CPR and size reduction experts WEIMA and Conair recovered and recycled all production scrap at NPE2024.
Read MoreMaking the Circular Economy a Reality
Driven by brand owner demands and new worldwide legislation, the entire supply chain is working toward the shift to circularity, with some evidence the circular economy has already begun.
Read MorePeople 4.0 – How to Get Buy-In from Your Staff for Industry 4.0 Systems
Implementing a production monitoring system as the foundation of a ‘smart factory’ is about integrating people with new technology as much as it is about integrating machines and computers. Here are tips from a company that has gone through the process.
Read More