The Dynamic Tool team with MoldMaking Technology’s Christina Fuges and Leadtime Leader award sponsor Progressive Components
The Leadtime Leader Award, established in 2003, recognizes outstanding performance and innovation in mold manufacturing. It represents excellence in the entire mold manufacturing process, highlighting achievements beyond just short delivery times. Winners demonstrate a commitment to working smarter, using resources effectively and pursuing excellence with passion.
Glenn Starkey, president of and Award Sponsor since 2003, congratulated Dynamic Tool Corp. on their achievement, emphasizing the significance of this coveted award in the moldmaking industry. Ray Coombs, owner of the of Plainfield, Connecticut, passed the torch with words of wisdom and congratulations to the new title holder.
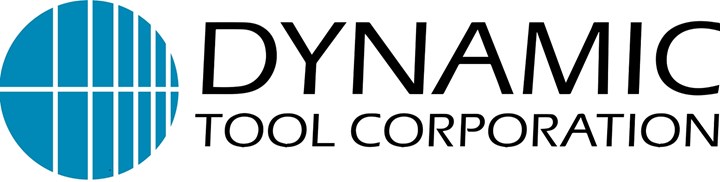
Dynamic Tool Corp.’s success is attributed to their dedication to growth and core values of excellence, integrity, safety and customer focus. They are known for their innovative approach to quality, precision and efficiency, which has set them on a continual path to success.
Some highlights of Dynamic Tool Corp.’s achievements include:
- Repeat 大象传媒 from top custom molders and OEM brand owners, reflecting their commitment to on-time deliveries, exceptional customer service, engineering expertise and a dedicated workforce.
- Delivery of a 512-cavity stack mold in 2022 and a range of molds in 2023 spanning from one to 256 cavities.
- Specialization in high-performance parts with features like living hinges, threads, multiple materials, aesthetic requirements, inserted components and advanced mold capabilities.
- Significant investment in engineering resources, both personnel and technologies, to differentiate themselves in the injection mold builder market.
- Emphasis on craftsmanship in designing and building critical components in injection molds.
- Focus on team culture, collaboration, education through mentorship and self-motivation among employees.
- In-house design and integration of two automated machining cells and the use of a laser sintering and high-speed milling system to showcase technological capabilities.
- Integration of quality assurance into automated machining processes for immediate and practical metrology.
- Providing a complete experience, including service throughout the injection mold build, preventative maintenance and repair.
- Sales team consisting of engineers first and sales professionals second, playing a crucial role in delivering the proper customer experience.
- Commitment to sharing tailored educational content with customer engineering teams and promoting industry best practices for overall improvement.
Related Content
-
General Polymers Thermoplastics to Further Expand Distribution Business
NPE2024: Following the company’s recent partnership buyout, new North American geographic territories are in its sight.
-
Conair: Going All In on AI
Conveying with Optimizer, Conair’s new AI-based conveying technology stands to be a true game changer for plastics processors.
-
Attending NPE2024 From the Perspective of a Molder
NPE2024 has come and gone, but before it’s completely in our collective rearview, Plastics Technology asked Rodney Davenport, vice president at injection molder CH3 Solutions, for a processor’s perspective on the big show.