DeDuster Systems Cleans Up rPET Sheet
rPlanet cut its gel count drastically—allowing it to sell more sheet at prime prices—after installing a DeDuster system.
Gels were not on ’s radar when the vertically integrated rPET processor started up back in 2018. Under one roof at its 300,000+ ft2 plant in Vernon, Calif., rPlanet takes in bottles, clamshell containers, and other packaging waste from curbside collection; puts it through an extensive series of sorting and cleaning procedures; grinds it into flake and subjects it to rigorous washing and decontamination; raises the intrinsic viscosity (IV) of the material in accordance with end-use requirements; and processes it into food-grade sheet, thermoformed containers, and injection molded preforms for bottles.
But those nasty gels became an issue in rPlanet’s extruded sheet soon after the plant was started. Gels are visual defects that can be caused by a variety of factors. No one wants gels, so quality-control departments are trained to be on the lookout for them. They use industry-standard references to manually count gels, or expensive automated machines that can count them automatically. Rolls of sheet with out-of-spec gel counts are sold at a significantly discounted rate, or must be ground up for reuse, which hurts the bottom line.
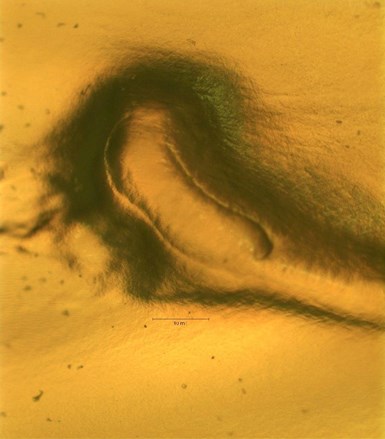
Gels are a common problem often caused by dusty, contaminated materials and the defects they cause can negatively impact the price a sheet processor can demand for its product. Photos: Pelletron Corp.
While gels can be caused by several different things, dust and other fine contaminates are high on the list. Recycled bottle flake is notoriously dusty because of the mechanical attrition inflicted during grinding, decontamination and the numerous material-handling steps that occur between the baled post-consumer bottles and the extrusion or injection molding machine.
So after discovering that gels were creating quality issues, rPlanet Earth decided to do something about it and contacted Pelletron Corp., Lancaster, Pa. Pelletron specializes in gentle pneumatic conveying and DeDuster systems for plastic processing. Pelletron was familiar with rPlanet’s operation because it had supplied rPlanet with its entire material-handling system from the wash line to the extruder and injection machines.
The Pelletron DeDuster systems use an electromagnetic flux-field coil to disturb fine dust stuck to the flake due to static electricity, along with counterflow air to separate dust and streamers from the flake. These systems can lower the dust content from over 2000 ppm concentration of particles up to 500-micron size to less than 200 ppm. Other dust-removal systems on the market cannot achieve that level of separation in a package as compact as the DeDuster, Pelletron maintains.
So rPlanet Earth purchased an XP45 DeDuster capable of handling 4410 lb/hr of rPET flake for each of its Welex-brand sheet lines, recalls Mac Schlicher, rPlanet Earth’s sr. process engineer. The low stack-up height of the DeDuster allowed it to be mounted atop the extruder throat, below the loss-in-weight feeders. Pelletron supplied the equipment and controls while rPlanet handled the electrical and mechanical installation.
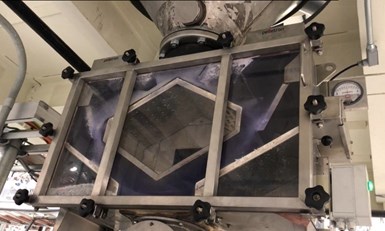
The low stack-up height of Pelletron’s DeDuster allowed it to be mounted atop the extruder throat, below the feeders.
The DeDusters did the trick; Schlicher says the incidence of gels diminished after the they were commissioned on the sheet extrusion lines. In a controlled study on one line, up to an average of one gel (0.2-1.0 mm²) was counted for every meter (3.28 ft) of sheet extruded when the DeDuster was off. That count made the sheet off-spec for rPlanet’s more persnickety customers. Turning the DeDuster on reduced the gel count to an average of 0.17 gels in the same size range per meter of sheet. That was on spec, meaning the sheet could be sold at prime rate.
Pelletron’s DeDuster systems are available in capacities from 50 to 330,000 lb/hr. The company offers free testing to demonstrate how well the unit can clean a particular material.
Related Content
Breaking News From NPE2024
Here is a firsthand report of news in injection molding, extrusion, blow molding and recycling not previously covered.
Read MoreMultilayer Solutions to Challenges in Blow Molding with PCR
For extrusion blow molders, challenges of price and availability of postconsumer recycled resins can be addressed with a variety of multilayer technologies, which also offer solutions to issues with color, processability, mechanical properties and chemical migration in PCR materials.
Read MoreHow to Extrusion Blow Mold PHA/PLA Blends
You need to pay attention to the inherent characteristics of biopolymers PHA/PLA materials when setting process parameters to realize better and more consistent outcomes.
Read MorePlastics Technology Year in Review: Your Favorite Reads of 2024
A year-end review of the top stories showcasing industry trends, advancements and expert insights. Revisit the articles that captured the attention of the plastics community.
Read MoreRead Next
Beyond Prototypes: 8 Ways the Plastics Industry Is Using 3D Printing
Plastics processors are finding applications for 3D printing around the plant and across the supply chain. Here are 8 examples to look for at NPE2024.
Read MoreSee Recyclers Close the Loop on Trade Show Production Scrap at NPE2024
A collaboration between show organizer PLASTICS, recycler CPR and size reduction experts WEIMA and Conair recovered and recycled all production scrap at NPE2024.
Read MorePeople 4.0 – How to Get Buy-In from Your Staff for Industry 4.0 Systems
Implementing a production monitoring system as the foundation of a ‘smart factory’ is about integrating people with new technology as much as it is about integrating machines and computers. Here are tips from a company that has gone through the process.
Read More