Captive Molder Beefs Up Auxiliaries to Boost Quality, Consistency
SeeScan adds conveying, drying, feeding and chilling technologies to improve quality — and enhance employee safety — in production of its underground/underwater inspection systems.
A captive molder recently made sweeping changes to its fleet of auxiliary equipment and as a resulted achieved a completely integrated system that improved the quality and consistency of its molded parts while significantly enhancing operator safety.
Based in San Diego, makes a wide range of vision systems and instruments that help locate utilities and inspect pipes in what the company describes as a mission “to make the underground visible.” At a 120,000-ft2 facility, SeeScan molds its own parts on eight injection presses of 20 to 330 tons. It runs a gamut of engineering thermoplastics, including ABS, PC, nylon and PEI, either neat or glass-filled in a range of colors.
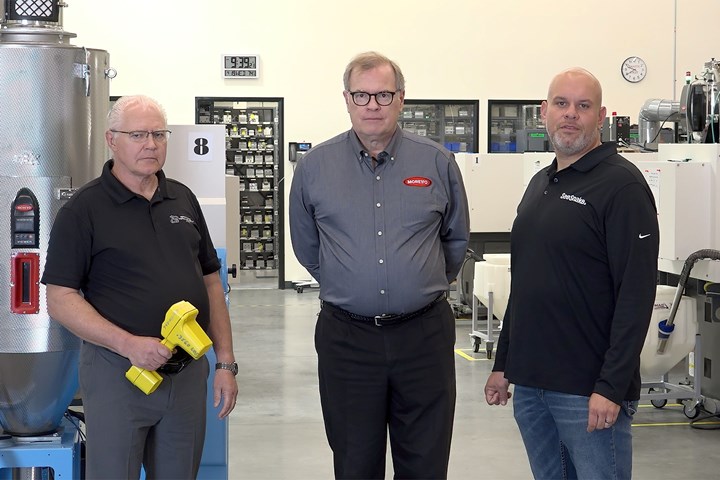
L-r: Martyn Bramhall of Bramac Machinery; Mike Mueller, Moretto regional sales manager; Kirk Joy, SeeScan director of tooling. (Photos: Moretto)
Last year the company initiated a project aimed at upgrading the auxiliary equipment in its plant, with the objective to address some inefficiencies with its previous machines and add more automation to the process, relying less on operators to move materials around. It decided on , adding eight new dryers and conveying systems, three loss-in-weight gravimetric feeders and a new temperature-control system.
Solving a Resin Moisture Problem
On the drying side, SeeScan was using a rack-mounted central system that was especially problematic on overnight runs. Explains SeeScan’s Director of Tooling Kirk Joy, “Before the night shift, we would transport enough material to the presses to satisfy an overnight run. But we noticed as time progressed that we would be picking up moisture in the process. The parts we made at the beginning of the evening were not the same as those throughout the evening and into the morning.”
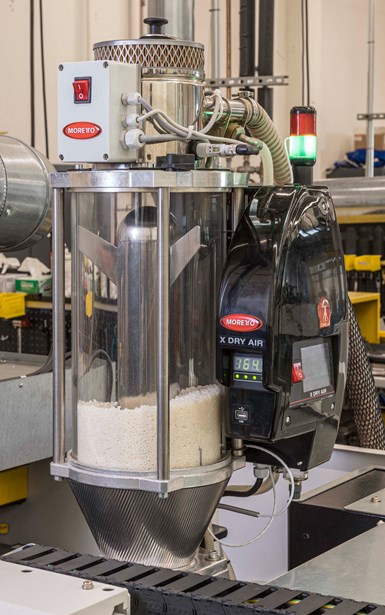
SeeScan uses Moretto feedthroat-mounted compressed-air mini dryers for applications requiring 12 lb/hr or less.
After consulting with Moretto’s West Coast sales representative, Martyn Bramhall of Bramac Machinery, SeeScan bought three different styles of Moretto dryers. These included the feedthroat XD Mini Series compressed-air dryer, which SeeScan deployed on smaller presses for micromolding jobs; XComb wheel dryers; and XD cabinet dryers. All Moretto dryers come with anti-stress (over-drying protection) as standard, notes Mike Mueller, Moretto regional sales manager.
“We do everything from micromolding to running parts requiring a 330-ton press,” Joy explains. “The fact that Moretto has a variety of drying technologies to address our needs and to help us improve consistency has been advantageous. And providing us the ability to drying without having to worry about overstressing our materials during long production runs was one of the key technologies that stood out to us. That feature has also allowed us to save lot on energy,” he adds, which nowadays is critical virtually everywhere but particularly in high-cost states like California.
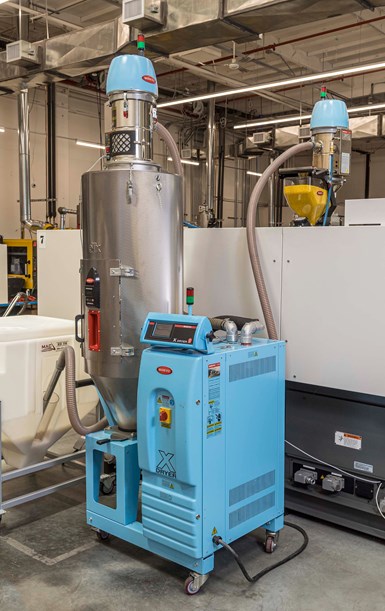
Cart-mounted cabinet dryers are for applications requiring 20 lb/hr, or higher if furnished with a VFD turbo compressor.
Controlling Color Consistency
Along with drying challenges, SeeScan was looking to upgrade from a labor-intensive color-feeding process. Says Joy, “We had previously been mixing color concentrate with virgin resin manually. An operator would fill the material into bucket, add the color concentrate at the desired letdown ratio, then we’d mix it and put in into the cold hopper. This process was creating a number of issues. At the top of the list was employee health and safety; our operators were regularly handling and picking up barrels of material.” SeeScan went with a trio of Moretto’s DPK gravimetric loss-in-weight color feeders.
“The color feeder has enabled us to maintain consistency through a very accurate dosage of color concentrate with virgin materials and it does so automatically, so there is no manual handling of materials,” says Joy. The units also self-tune to account for bulk-density variations in the material, adds Mueller.
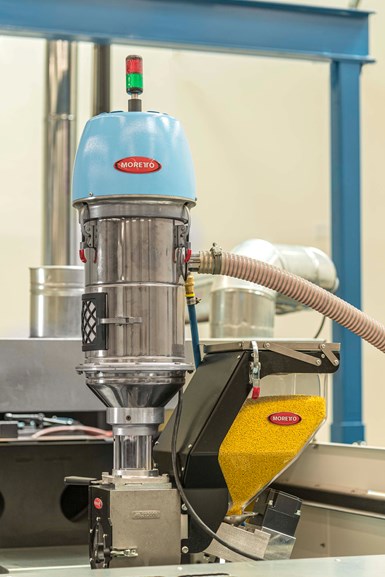
DPK loss-in-weight color feeders helped SeeScan automate what had been a highly labor-intensive process.
In addition to the three feeders, SeeScan bought additional hoppers that it keeps filled with color on the shelf. “This allows us to store our color concentrate without worrying about any debris infiltration and allows for ultra-fast color changes. All we need to do is purge, switch the hoppers, and we’re ready to go,” says Joy.
“We are able to decrease scrap significantly because of the accuracy and consistency provided by the feeder,” he adds. “The machine-mounted color feeder also integrates well with our process. It doesn’t take up any floor space and doesn’t get in our way when we want to hang tooling.”
Meantime, SeeScan added Moretto’s TWP12S High Temp water-temperature control unit, which Joy says is ideal for this plant because it runs so many high-temperature materials: “With high-temperature materials, a lot of times the water temperature will run up to 320° F. That will ruin conventional pump seals. This TCU has a magnetically coupled pump, so there is no pump seal. It also has all-solid-state controls, which is helpful.”
“The fact that Moretto has a variety of drying technologies to address our needs and to help us improve consistency has been advantageous.”
States Joy, “With Moretto, what we ended up with was a completely integrated solution — from conveying material to blending, drying and more— that has improved our consistency and reliability and significantly enhances operator safety.”

Related Content
For Extrusion and Injection-Blow Molders, Numerous Upgrades in Machines and Services
Uniloy is revising its machinery lines across the board and strengthening after-sales services in tooling maintenance, spare parts and tech service.
Read MorePolyJohn Turns to Blow Molding, Doubles Its Productivity
Leading maker of portable sanitation products knew thermoforming, sheet extrusion, rotomolding and injection molding. Then it found the missing link to higher productivity and new markets: blow molding.
Read MoreNPE2024 Materials: Spotlight on Sustainability with Performance
Across the show, sustainability ruled in new materials technology, from polyolefins and engineering resins to biobased materials.
Read MoreNPE2024 Wrap-Up: Sustainability Dominates Show Floor News
Across all process types, sustainability was a big theme at NPE2024. But there was plenty to see in automation and artificial intelligence as well.
Read MoreRead Next
Beyond Prototypes: 8 Ways the Plastics Industry Is Using 3D Printing
Plastics processors are finding applications for 3D printing around the plant and across the supply chain. Here are 8 examples to look for at NPE2024.
Read MoreSee Recyclers Close the Loop on Trade Show Production Scrap at NPE2024
A collaboration between show organizer PLASTICS, recycler CPR and size reduction experts WEIMA and Conair recovered and recycled all production scrap at NPE2024.
Read More