Revisiting the '5 M's' of Molding
All injection molding ultimately comes down to the “Man, Mold, Machine, Material and Method.” But those key aspects can be viewed differently if you’re auditing mold changes before startup or troubleshooting changes for an already validated process.
Injection molding can be a real challenge if you don’t follow the “Five M’s”: Man, Mold, Machine, Material and Method. Our goal of 100% efficiency, zero scrap and repeatable processes can sometimes be hindered by poor setups or changes in the molding process.
Over the years, I have developed two separate “5M” systems. One applies to auditing mold changes before startup, while the second applies to troubleshooting changes within a validated process. This article will explain the application of both systems and how they can be used to consistently identify and correct molding problems.
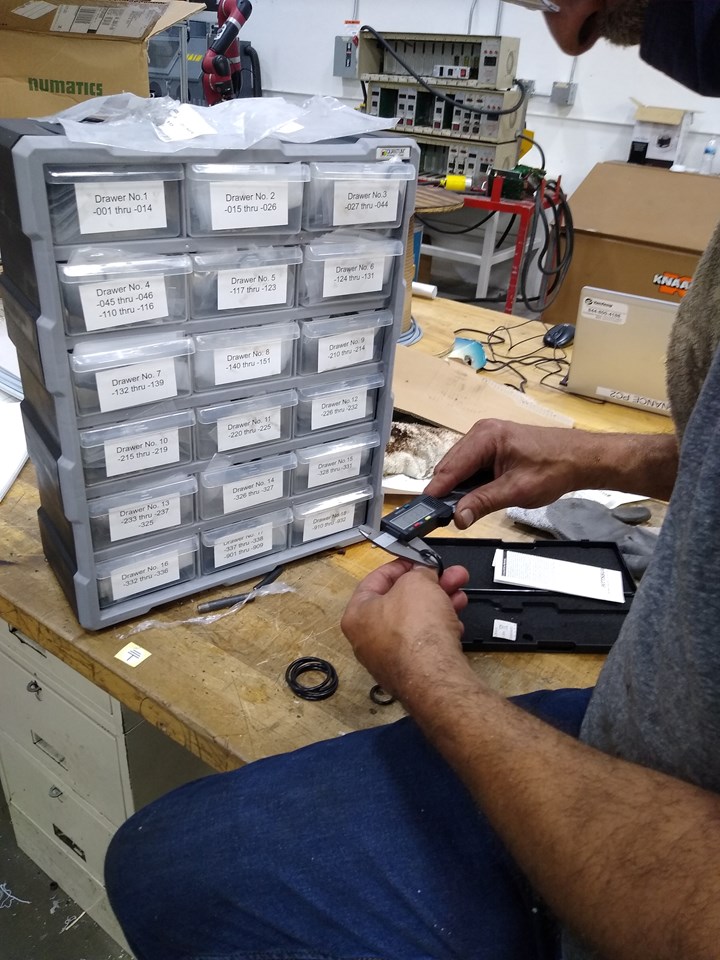
The second “M” is Mold: A worker verifies the diameter of an o-ring prior to its installation.
(Photo: Garrett MacKenzie)
Auditing a Mold Change
This 5M configuration is used when auditing a mold change before startup. It serves as an outline for the entire audit process, and if it is repeated every time a mold change is audited, it can help prevent poor setups leading to poor startups. Here are the steps taken for each:
Man: This applies to area setup and notification of the supervisor that the press is about to start. This gives the supervisor time to schedule the operator and get him or her into place when parts start moving down the belt. Cell layout is verified as being correct for the new job. All old packaging, labels and components are verified as removed from area, and all required components are confirmed to be in place.
Mold: It is now time to inspect all stages of the mold setup. The mold should be clean and ready to start. Clamp speeds should be verified. Mold components should be inspected for damage and proper working condition. Water should be verified as on, and hoses checked for proper placement and flow. Low-pressure close should also be verified. Hot-runner cables should be verified as properly connected, and hot-runner and mold temperature setpoints and actuals should be examined. You must verify core hookups and operation, as well as valve-gate hookup, operating them manually to assure readiness.
Machine: This refers to all mechanicals, including auxiliaries. Verify correct robot end-of-arm-tooling (EOAT), and that the corresponding robot program is loaded. Check all auxiliaries for readiness and proper operation. Verify that the dryer is on and at the correct temperature. Ensure the correct screw tip is installed.
Material: Verify that the correct material has been loaded, and that no other materials are present. Check to see color feeders are set properly and make sure the press has been purged thoroughly and is ready for operation. This includes ensuring that the barrel temperatures are correct and the actuals match the setpoints. Verify that the material purged looks clean and isn’t exhibiting any signs of moisture.
Method: This refers to the process, which should be verified as conforming to the setup sheet that was developed when the process was validated. At a minimum, temperatures, shot size, transfer position, hold pressure and injection speeds should be certified as correct.
Using the 5M’s, we are given a direct path for inspection that is thorough and improves our ability to quickly audit or troubleshoot problems and poor setup practices.
Troubleshooting a Validated Process
When troubleshooting, the 5 M’s change slightly. Method is exchanged for Maintenance. Why? The first steps of troubleshooting are cleaning/inspecting the mold and verifying that the process (method) is correct. This should be automatic. Once completed, the 5M’s again come into play.
The same inspections are performed as noted earlier in the article, only now the processor is looking for what has changed. Is the operator causing a defect? Has something changed with the mold? Could a change have occurred with the material we are using? Is the press functioning properly, or do I need to get maintenance involved?
Using the 5M’s, we are given a direct path for inspection that is thorough and improves our ability to quickly audit or troubleshoot problems and poor setup practices. As we develop our approach, our auditing practices become stronger, which reduces downtime and scrap. Tools such as these not only improve our odds of success, but they also boost the profitability of the companies we represent.
ABOUT THE AUTHOR: Garrett MacKenzie is the owner/editor of plastic411.com, as well as a consultant/trainer in plastic injection molding. He has provided process-engineering expertise to many top companies, including Glock, Honda, Johnson Controls and Rubbermaid, and currently works for a company that provides automotive products to Yenfeng, Faurecia and other top automotive suppliers. Contact: garrett@plastic411.com.
Related Content
Understanding the Effect of Pressure Losses on Injection Molded Parts
The compressibility of plastics as a class of materials means the pressure punched into the machine control and the pressure the melt experiences at the end of fill within the mold will be very different. What does this difference mean for process consistency and part quality?
Read MoreThe Fundamentals of Artificial Intelligence and Machine Learning and Their Application to Injection Molding
As AI and ML continue to develop, they can eventually play a role in helping molders predict more accurately and, perhaps someday, model very close to the actual process results.
Read MoreUsing Data to Pinpoint Cosmetic Defect Causes in Injection Molded Parts
Taking a step back and identifying the root cause of a cosmetic flaw can help molders focus on what corrective actions need to be taken.
Read MoreInjection Molding: Focus on these Seven Areas to Set a Preventive Maintenance Schedule
Performing fundamental maintenance inspections frequently assures press longevity and process stability. Here’s a checklist to help you stay on top of seven key systems.
Read MoreRead Next
The 5 M’s of Molding—Part I: Man (labor)
There are many areas in which personnel affect consistency and repeatability within a plastics operation.
Read MoreQuick Changeover: The 3-to-7-Minute Color Change
Step 1: Assessment—These questions must be asked during the development of fast changeover procedures.
Read More